Perang dikenal sebagai mesin kemajuan terbaik. Industri tank Uni Soviet membuat lompatan kualitatif yang memusingkan hanya dalam beberapa tahun perang. Mahkota sebenarnya dari ini adalah tank seri IS.
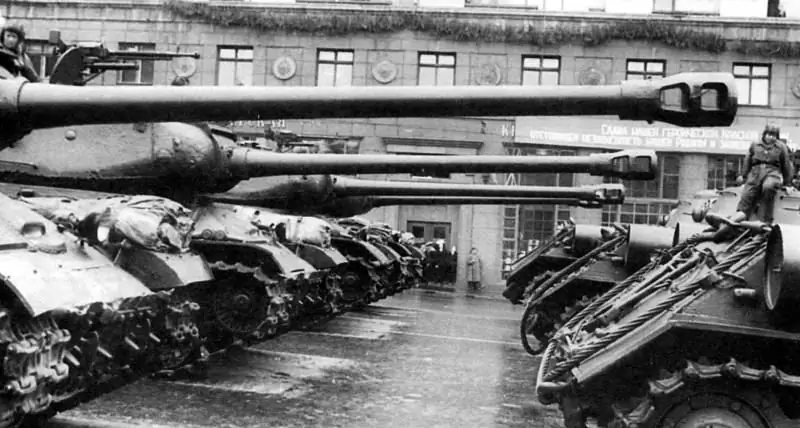
resep Magnitogorsk
Di bagian cerita sebelumnya, itu tentang armor cor kekerasan tinggi 70L yang digunakan untuk menara tank IS. Pengembang baju besi dari TsNII-48 jauh dari pengalaman pertama dalam menciptakan perlindungan untuk tank berat.
Sebelum Kursk Bulge, yang menjadi katalis untuk pengembangan bangunan tangki berat domestik, objek utama modernisasi adalah tangki KV. Awalnya, semua pekerjaan ditujukan untuk mengurangi proporsi aditif paduan yang langka dalam komposisi baju besi. Bahkan nama di TsNII-48 muncul dengan nama yang sesuai - baja paduan ekonomis. Armor asli merek FD-7954, yang digunakan tank KV untuk memasuki Perang Patriotik Hebat, mengandung, menurut persyaratan teknis, hingga 0,45% molibdenum, 2,7% nikel dan kromium.
Pada akhir 1941, sekelompok peneliti yang dipimpin oleh Andrei Sergeevich Zavyalov di Institut Lapis Baja menciptakan resep untuk baja FD-6633 atau 49C, di mana molibdenum membutuhkan tidak lebih dari 0,3%, kromium - hingga 2,3%, dan nikel - sampai 1, 5%. Mempertimbangkan bahwa tangki seri KV dari paruh kedua tahun 1941 hingga 1943 dikumpulkan sekitar 4 ribu eksemplar, orang dapat membayangkan jumlah penghematan nyata dalam logam paduan.
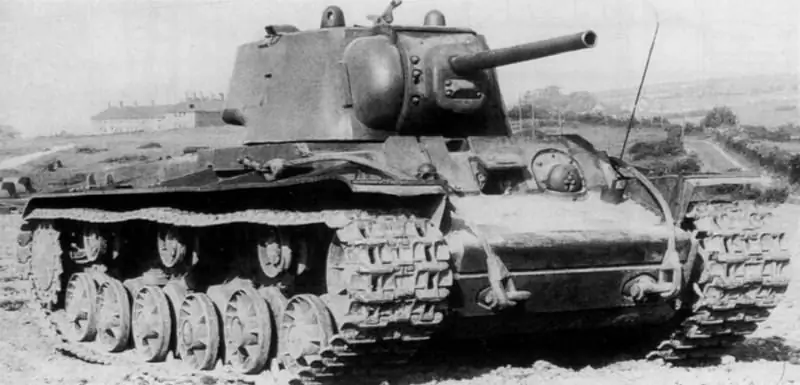
Rahasia sukses
Rahasia keberhasilan ahli metalurgi terletak pada studi tentang parameter pembentukan fraktur berserat dari baju besi - parameter utama ketahanan proyektil. Ternyata Anda dapat melakukannya tanpa proporsi elemen paduan yang signifikan hanya dengan mengubah laju pendinginan pelindung selama pendinginan. Tapi ini sederhana dalam kata-kata - berapa banyak percobaan pendahuluan dan ahli metalurgi leleh harus dilakukan, hanya arsip yang sekarang diklasifikasikan yang dapat mengetahuinya.
Di Pabrik Metalurgi Magnitogorsk pada tahun 1941, prototipe pertama baja 49C diperoleh, yang tidak kalah dengan baju besi "pra-perang" tradisional. Secara khusus, penembakan oleh meriam 76 mm menunjukkan kepatuhan penuh terhadap persyaratan taktis untuk tank. Dan sejak 1942, hanya baju besi dengan nama 49C yang digunakan untuk seri KV. Perlu diingat bahwa konsumsi kromium, molibdenum, dan nikel telah menurun secara signifikan.
Pencarian formulasi baru baju besi untuk alat berat tidak berhenti sampai di situ. Pada tahun 1942 baja GD-63-3 "dilas", sama sekali tanpa kromium dan nikel yang langka. Sampai batas tertentu, nikel digantikan oleh mangan - bagiannya meningkat lebih dari tiga kali (hingga 1,43%). Prototipe baju besi baru ditembakkan. Dan mereka ternyata sangat cocok untuk penggunaan massal dalam desain KV. Tetapi tank Klim Voroshilov dengan armor kekerasan sedang sedang pensiun. Dan tempat kendaraan berat diambil oleh kendaraan "Joseph Stalin" dengan baju besi kekerasan tinggi.
Armor gulung 51C
Jika armor 70L untuk turret IS-2 dapat dilemparkan, maka trik ini tidak akan berhasil dengan bagian lambung tangki. Di sini, para insinyur menghadapi dua masalah sekaligus - pembuatan baju besi dengan ketebalan tinggi dan kebutuhan untuk mengelasnya menjadi lambung yang sudah jadi.
Setiap orang yang tertarik mungkin sudah mengetahui masalah yang disebabkan oleh pengelasan baju besi T-34 - ada kemungkinan besar retak di area las. IS-2 tidak terkecuali. Dan tubuhnya pada awalnya seharusnya dimasak dari bagian yang akhirnya diberi perlakuan panas.
Menyadari kesulitan dan bahaya apa yang akan ditimbulkan oleh solusi teknologi semacam itu dalam operasi militer, spesialis TsNII-48 mengubah siklus produksi tank. Akibatnya, pada tahun 1943, di Pabrik Pembuatan Mesin Berat Ural dan Pabrik Chelyabinsk No. 200, lambung IS-2 diputuskan untuk dimasak dari pelat baja yang hanya melewati liburan tinggi setelah bergulir. Artinya, pada kenyataannya, lambung tangki berat dirakit dari baja "mentah". Ini sangat mengurangi cacat pengelasan pada baja canai kekerasan tinggi 51C.
Perlakuan panas terakhir dengan pemanasan sebelum pendinginan sudah dilakukan pada badan tangki yang dilas, setelah sebelumnya memperkuatnya dengan penyangga internal. Jenazah disimpan dalam oven selama tiga jam. Dan kemudian, pada perangkat khusus, mereka dipindahkan ke tangki pendingin air dan disimpan di dalamnya selama 15 menit. Selain itu, suhu air di tangki pendinginan naik dari 30 menjadi 55 ° C. Suhu permukaan tubuh setelah dikeluarkan dari air adalah 100-150 °. Dan itu tidak semua.
Setelah pendinginan, tubuh segera mengalami temper rendah dalam tungku sirkulasi pada suhu 280-320 ° dengan penahanan setelah mencapai suhu ini selama 10-12 jam. Temperatur rendah menara cor dari baju besi 70L dilakukan dengan cara yang sama. Menariknya, kontrol retak pada lambung IS-2 eksperimental berlangsung selama empat bulan, ketika tangki produksi pertama meninggalkan gerbang pabrik.
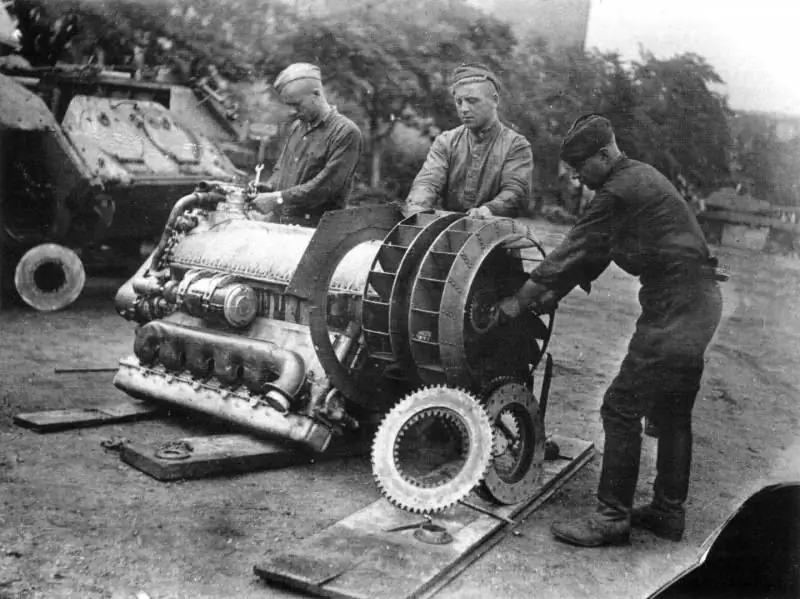
Komposisi kimia
Apa saja Rolled Armor 51C yang menjadi andalan IS-2, ISU-122 dan ISU-152? Ini adalah baja pengerasan dalam untuk ketebalan armor besar dengan komposisi kimia berikut (%):
C 0, 18-0, 24
Mn 0, 70-1, 0
Si 1, 20-1, 60
Cr 1, 0-1, 5
Ni 3.0-3.8
Mo 0, 20-0, 40
P 0,035
S 0,035.
Dibandingkan dengan baja tuang 70L, baja canai 51C memiliki proporsi molibdenum dan nikel yang lebih tinggi, yang menjamin peningkatan kemampuan pengerasan hingga 200 mm. Ketika lambung tank berat ditembakkan dengan cangkang 88 mm, ternyata baju besi dengan kekerasan tinggi jauh lebih unggul dalam daya tahan dibandingkan pendahulunya dengan kekerasan sedang. Masalah penempatan baju besi yang digulung 51C segera diselesaikan.
Pengelasan cerdas
Kontribusi penting bagi keberhasilan pengembangan produksi lapis baja tank seri IS dibuat dengan pengelasan baja otomatis di bawah lapisan fluks. Karena tidak mungkin untuk mentransfer seluruh proses pembuatan lambung lapis baja tangki ke pengelasan seperti itu pada awal 1944, para insinyur berfokus pada mengotomatisasi lapisan yang paling panjang dan dimuat secara mekanis.
Di pabrik Chelyabinsk No. 200, dalam proses perakitan lambung tangki berat IS-2, hanya 25% dari semua pengelasan yang dapat diotomatisasi. Pada pertengahan 1944, Tankograd mampu mengotomatisasi 18% dari semua kemungkinan 25% dari lasan. Panjang total jahitan yang dilas di sepanjang lambung tangki berat IS-2 adalah 410 meter berjalan, di mana 80 meter berjalan dilakukan dengan metode pengelasan otomatis.
Hasil ini telah menyebabkan penghematan yang signifikan dalam sumber daya yang langka dan listrik. Dimungkinkan untuk membebaskan hingga 50 tukang las manual yang memenuhi syarat (biaya tenaga kerja mereka sebesar 15.400 jam kerja) dan menghemat 48.000 kilowatt-jam listrik. Penurunan konsumsi elektroda (sekitar 20.000 kg, austenitik - 6.000 kg), oksigen (sebesar 1.440 meter kubik).
Waktu yang dihabiskan untuk pengelasan juga telah berkurang secara signifikan. Misalnya, pengelasan bagian bawah dan kotak turret ke samping dengan jahitan enam belas meter membutuhkan 9,5 jam kerja dalam mode manual, dan hanya 2. Jahitan yang sama panjangnya yang menghubungkan bagian bawah ke sisi lambung tangki dalam mode otomatis diperlukan 3 jam kerja (langsung manual 11, 4). Pada saat yang sama, tukang las yang sangat terampil dapat digantikan oleh pekerja tidak terampil dalam pengelasan otomatis.
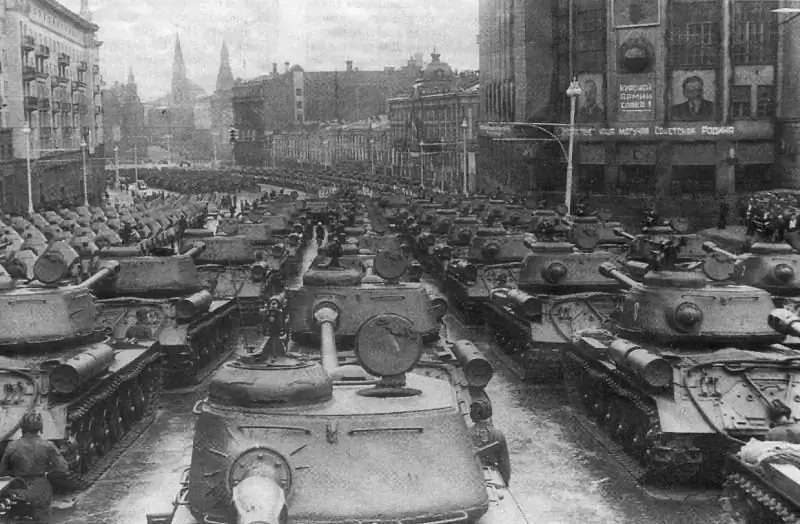
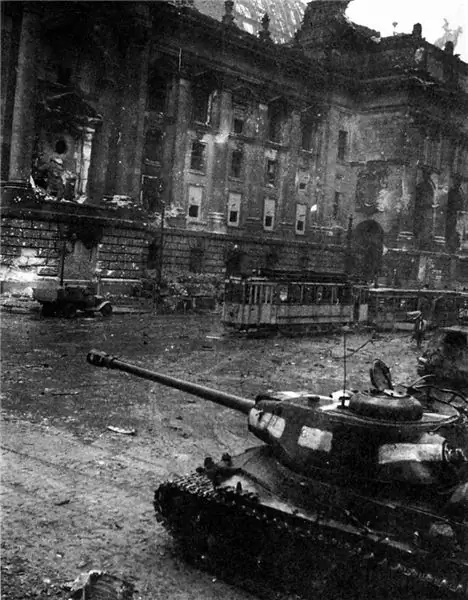
SAG Ural
Peneliti industri tank Soviet, kandidat ilmu sejarah Zapariy Vasily Vladimirovich dari Institut Sejarah dan Arkeologi Cabang Ural dari Akademi Ilmu Pengetahuan Rusia dalam salah satu karyanya menjelaskan dengan sangat rinci unit pengelasan otomatis yang digunakan di Ural untuk lapis baja produksi lambung.
Yang paling luas adalah senapan serbu tipe "ACC" dengan kepala Bushtedt. Ada delapan instalasi seperti itu di Uralmash. Kecepatan umpan kawat di mesin ini tergantung pada tegangan di busur. Untuk itu diperlukan 5 unit, termasuk 3 motor listrik kinematik dan 1 motor generator.
Pada pertengahan tahun 1943, mesin las SA-1000 dirancang untuk kebutuhan tangki berat IS-2. Atau mesin las dengan kapasitas hingga 1000 A.
Untuk menguasai produksi lambung lapis baja untuk tank berat baru Chelyabinsk IS-3, para insinyur pabrik pada tahun 1944 merancang peralatan "SG-2000". Mesin ini dirancang untuk bekerja dengan kabel las rendah karbon dengan diameter yang meningkat (6-8 mm) dan menemukan aplikasinya dalam pembuatan menara IS-3. Instalasi memiliki dispenser untuk memasukkan komposisi khusus (berbagai ferroalloy) ke dalam bagian las untuk mendeoksidasi (mengembalikan) logam di dalamnya. Secara total, berdasarkan prinsip pengaturan sendiri busur pengelasan di UZTM, pada tahun 1945, 9 instalasi pengelasan otomatis dari tiga jenis dibuat: "SA-1000", "SG-2000", "SAG" ("Pengelasan otomatis kepala").
Lebih cantik dari baju besi Jerman
Hasil dari keseluruhan cerita dengan baju besi tank berat IS adalah pengembangan resep baja yang sangat cepat yang melampaui baju besi Jerman dalam sifat taktisnya. TsNII-48 menerima baja 120 mm yang dapat dikeraskan, yang ketebalannya, jika perlu, dapat ditingkatkan menjadi 200 mm.
Ini menjadi fondasi utama untuk pengembangan keluarga tank berat Soviet pasca-perang.