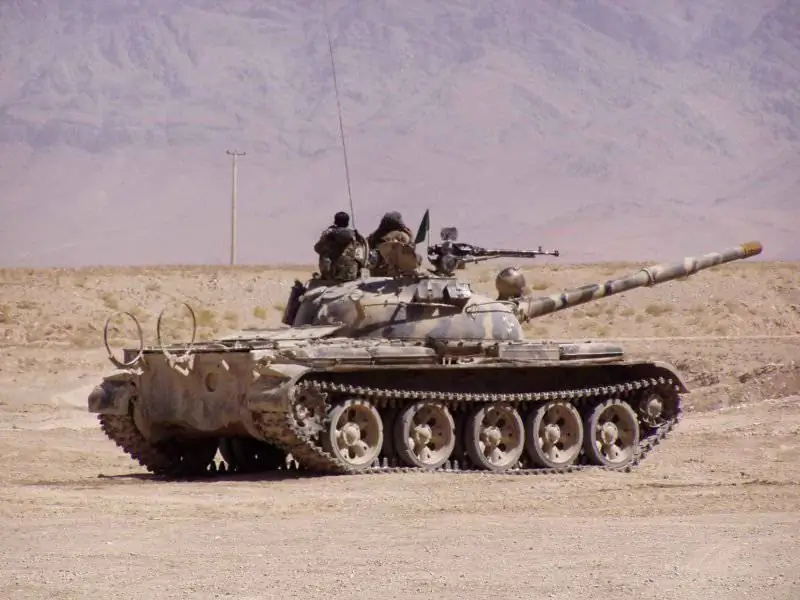
Pada tahun 1955, keputusan pemerintah dibuat untuk membuat biro desain untuk teknik diesel khusus di Pabrik Teknik Transportasi Kharkov dan untuk membuat mesin diesel tangki baru. Profesor A. D. Charomsky ditunjuk sebagai kepala desainer biro desain.

Pilihan skema desain mesin diesel masa depan ditentukan terutama oleh pengalaman bekerja pada mesin diesel 2-tak OND TsIAM dan mesin U-305, serta keinginan untuk memenuhi persyaratan perancang T baru. -64 tank, dikembangkan di pabrik ini di bawah kepemimpinan kepala desainer AA … Morozov: untuk memastikan dimensi minimum mesin diesel, terutama ketinggian, dalam kombinasi dengan kemungkinan menempatkannya di tangki dalam posisi melintang antara gearbox planet onboard. Skema diesel dua langkah dipilih dengan susunan horizontal lima silinder dengan piston bergerak berlawanan di dalamnya. Diputuskan untuk membuat mesin dengan inflasi dan pemanfaatan energi gas buang dalam turbin.
Apa alasan di balik pilihan mesin diesel 2-tak?
Sebelumnya, pada 1920-an-1930-an, pembuatan mesin diesel 2-tak untuk penerbangan dan kendaraan darat terhambat karena banyak masalah yang belum terselesaikan yang tidak dapat diatasi dengan tingkat pengetahuan, pengalaman, dan kemampuan industri dalam negeri yang dikumpulkan oleh waktu itu.
Studi dan penelitian mesin diesel 2-tak dari beberapa perusahaan asing mengarah pada kesimpulan tentang kesulitan yang signifikan untuk menguasainya dalam produksi. Jadi, misalnya, sebuah studi oleh Central Institute of Aviation Motors (CIAM) pada tahun 30-an mesin diesel Jumo-4 yang dirancang oleh Hugo Juneckers menunjukkan masalah signifikan yang terkait dengan pengembangan mesin tersebut dalam produksi mesin tersebut oleh domestik. industri periode itu. Diketahui juga bahwa Inggris dan Jepang, setelah membeli lisensi untuk mesin diesel ini, mengalami kegagalan dalam pengembangan mesin Junkers. Pada saat yang sama, di tahun 30-an dan 40-an, pekerjaan penelitian pada mesin diesel 2-tak sudah dilakukan di negara kita dan sampel eksperimental dari mesin tersebut dibuat. Peran utama dalam pekerjaan ini adalah milik spesialis CIAM dan, khususnya, Departemen Mesin Minyak (OND). CIAM merancang dan memproduksi sampel mesin diesel 2 langkah dengan berbagai dimensi: OH-2 (12/16, 3), OH-16 (11/14), OH-17 (18/20), OH-4 (8/ 9) dan sejumlah mesin asli lainnya.
Di antara mereka adalah mesin FED-8, yang dirancang di bawah bimbingan ilmuwan mesin terkemuka B. S. Stechkin, N. R. Briling, A. A. Bessonov. Itu adalah mesin diesel pesawat 2-tak 16 silinder berbentuk X dengan distribusi gas katup-piston, dengan dimensi 18/23, mengembangkan kekuatan 1470 kW (2000 hp). Salah satu perwakilan dari mesin diesel 2-tak dengan supercharging adalah mesin diesel turbo-piston 6 silinder berbentuk bintang dengan kapasitas 147 … 220 kW (200 … 300 hp) yang diproduksi di CIAM di bawah kepemimpinan BS Stechkin. Kekuatan turbin gas ditransmisikan ke poros engkol melalui gearbox yang sesuai.
Keputusan yang diambil saat membuat mesin FED-8 dalam hal ide itu sendiri dan skema desain kemudian mewakili langkah maju yang signifikan. Namun, proses kerja dan terutama proses pertukaran gas pada tekanan tinggi dan loop blowing belum dilakukan sebelumnya. Oleh karena itu, diesel FED-8 tidak menerima pengembangan lebih lanjut dan pada tahun 1937 pengerjaannya dihentikan.
Setelah perang, dokumentasi teknis Jerman menjadi milik Uni Soviet. Dia jatuh ke dalam A. D. Charomsky sebagai pengembang mesin pesawat, dan dia tertarik dengan koper Junkers.
Koper Junkers - serangkaian mesin turbo-piston dua langkah pesawat Jumo 205 dengan piston yang bergerak berlawanan diciptakan pada awal 30-an abad kedua puluh. Ciri-ciri mesin Jumo 205-C adalah sebagai berikut: 6 silinder, 600 hp. langkah 2 x 160 mm, perpindahan 16,62 liter, rasio kompresi 17: 1, pada 2.200 rpm
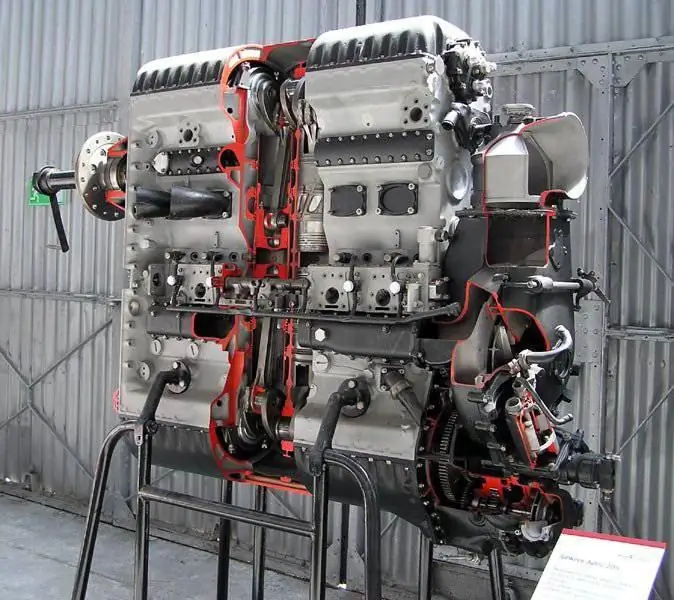
Mesin Jumo 205
Selama perang, sekitar 900 mesin diproduksi, yang berhasil digunakan pada pesawat amfibi Do-18, Do-27, dan kemudian kapal berkecepatan tinggi. Segera setelah berakhirnya Perang Dunia Kedua pada tahun 1949, diputuskan untuk memasang mesin seperti itu di kapal patroli Jerman Timur, yang beroperasi hingga tahun 60-an.
Atas dasar perkembangan ini, AD Charomsky pada tahun 1947 di Uni Soviet menciptakan pesawat dua langkah diesel M-305 dan kompartemen silinder tunggal dari mesin U-305 ini. Mesin diesel ini mengembangkan kekuatan 7350 kW (10.000 hp) dengan berat jenis rendah (0, 5 kg / h.p.) Dan konsumsi bahan bakar spesifik rendah -190 g / kWh (140 g / h.p.h). Susunan berbentuk X dari 28 silinder (empat blok 7 silinder) diadopsi. Dimensi mesin dipilih sama dengan 12/12. Dorongan tinggi disediakan oleh turbocharger yang terhubung secara mekanis ke poros diesel. Untuk memeriksa karakteristik utama yang ditetapkan dalam proyek M-305, untuk mengerjakan proses kerja dan desain suku cadang, model eksperimental mesin dibangun, yang memiliki indeks U-305. G. V. Orlova, N. I. Rudakov, L. V. Ustinova, N. S. Zolotarev, S. M. Shifrin, N. S. Sobolev, serta para teknolog dan pekerja pabrik percontohan CIAM dan bengkel OND.
Proyek pesawat full-size diesel M-305 tidak dilaksanakan, karena pekerjaan CIAM, seperti seluruh industri penerbangan tanah air, pada waktu itu sudah fokus pada pengembangan mesin turbojet dan turboprop dan kebutuhan untuk Mesin diesel 10.000 tenaga kuda untuk penerbangan menghilang.
Indikator tinggi diperoleh pada mesin diesel U-305: tenaga mesin liter 99 kW / l (135 hp / l), tenaga liter dari satu silinder hampir 220 kW (300 hp) pada tekanan dorongan 0,35 MPa; kecepatan rotasi tinggi (3500 rpm) dan data dari sejumlah pengujian mesin jangka panjang yang berhasil - mengkonfirmasi kemungkinan pembuatan mesin diesel 2-tak berukuran kecil yang efektif untuk keperluan transportasi dengan indikator dan elemen struktural yang serupa.
Pada tahun 1952, laboratorium No. 7 (bekas OND) CIAM diubah oleh keputusan pemerintah menjadi Laboratorium Penelitian Mesin (NILD) dengan subordinasinya kepada Departemen Teknik Transportasi. Kelompok inisiatif karyawan - spesialis berkualifikasi tinggi dalam mesin diesel (G. V. Orlova, N. I. Rudakov, S. M. Shifrin, dll.), dipimpin oleh Profesor A. D. Charomsky, sudah berada di NILD (kemudian - NIID). mesin U-305 2-tak.
Diesel 5TDF
Pada tahun 1954, A. D. Charomsky mengajukan proposal kepada pemerintah untuk membuat mesin diesel tangki 2-tak. Proposal ini bertepatan dengan persyaratan kepala perancang tangki baru A. A. Morozov, dan A. D. Charomsky ditunjuk sebagai kepala desainer pabrik. V. Malyshev di Kharkov.
Karena biro desain motor tangki pabrik ini sebagian besar tetap berada di Chelyabinsk, A. D. Charomsky harus membentuk biro desain baru, membuat basis eksperimen, mendirikan produksi percontohan dan serial, dan mengembangkan teknologi yang tidak dimiliki pabrik. Pekerjaan dimulai dengan pembuatan unit silinder tunggal (OTsU), mirip dengan mesin U-305. Di OTsU, elemen dan proses mesin diesel tangki ukuran penuh masa depan sedang dikerjakan.
Peserta utama dalam pekerjaan ini adalah A. D. Charomsky, G. A. Volkov, L. L. Golinets, B. M. Kugel, M. A., Meksin, I. L. Rovensky, dan lainnya.
Pada tahun 1955, karyawan NILD bergabung dengan pekerjaan desain di pabrik diesel: G. V. Orlova, N. I. Rudakov, V. G. Lavrov, I. S. Elperin, I. K. Lagovsky dan spesialis NILD lainnya L. M. Belinsky, LI Pugachev, LSroninson, SM Shifrin melakukan pekerjaan eksperimental di OTsU di Pabrik Teknik Transportasi Kharkov. Ini adalah bagaimana 4TPD Soviet muncul. Itu adalah mesin yang berfungsi, tetapi dengan satu kelemahan - tenaganya hanya lebih dari 400 hp, yang tidak cukup untuk sebuah tangki. Charomsky memasang silinder lain dan mendapat 5TD.
Pengenalan silinder tambahan telah secara serius mengubah dinamika mesin. Ketidakseimbangan muncul yang menyebabkan getaran torsional yang intens dalam sistem. Pasukan ilmiah terkemuka Leningrad (VNII-100), Moskow (NIID) dan Kharkov (KhPI) terlibat dalam solusinya. 5TDF dibawa ke kondisi EKSPERIMENTAL, dengan coba-coba.
Dimensi mesin ini dipilih sama dengan 12/12, yaitu. sama seperti pada mesin U-305 dan OTsU. Untuk meningkatkan respons throttle mesin diesel, diputuskan untuk menghubungkan turbin dan kompresor secara mekanis ke poros engkol.
Diesel 5TD memiliki beberapa fitur berikut:
- daya tinggi - 426 kW (580 hp) dengan dimensi keseluruhan yang relatif kecil;
- peningkatan kecepatan - 3000 rpm;
- efisiensi tekanan dan pemanfaatan energi gas buang;
- tinggi rendah (kurang dari 700 mm);
- penurunan perpindahan panas 30-35% dibandingkan dengan mesin diesel 4-tak (aspirat alami) yang ada, dan, akibatnya, volume yang lebih kecil diperlukan untuk sistem pendingin pembangkit listrik;
- efisiensi bahan bakar yang memuaskan dan kemampuan untuk mengoperasikan mesin tidak hanya pada bahan bakar diesel, tetapi juga pada minyak tanah, bensin dan berbagai campurannya;
- lepas landas daya dari kedua ujungnya dan panjangnya yang relatif kecil, yang memungkinkan untuk merakit tangki MTO dengan susunan melintang mesin diesel antara dua girboks terpasang dalam volume yang jauh lebih kecil daripada dengan susunan memanjang mesin dan gearbox pusat;
- penempatan yang berhasil dari unit-unit seperti kompresor udara bertekanan tinggi dengan sistemnya sendiri, generator starter, dll.
Setelah mempertahankan pengaturan melintang motor dengan power take-off dua arah dan dua transmisi on-board planetary yang terletak di kedua sisi mesin, para perancang bergeser ke tempat kosong di sisi mesin, sejajar dengan gearbox, kompresor dan turbin gas, yang sebelumnya dipasang di 4TD di atas blok mesin. Tata letak baru memungkinkan untuk mengurangi separuh volume MTO dibandingkan dengan tangki T-54, dan komponen tradisional seperti girboks pusat, girboks, kopling utama, mekanisme ayun planetary onboard, penggerak akhir, dan rem dikeluarkan darinya. Sebagaimana dicatat kemudian dalam laporan GBTU, transmisi jenis baru menghemat 750 kg massa dan terdiri dari 150 suku cadang mesin, bukan 500 suku cadang sebelumnya.
Semua sistem servis mesin saling bertautan di atas mesin diesel, membentuk "lantai dua" MTO, skema yang dinamai "dua tingkat".
Performa tinggi mesin 5TD membutuhkan penggunaan sejumlah solusi fundamental baru dan material khusus dalam desainnya. Piston untuk diesel ini, misalnya, dibuat menggunakan bantalan panas dan pengatur jarak.
Cincin piston pertama adalah cincin api tipe bibir kontinu. Silinder terbuat dari baja, berlapis krom.
Kemampuan untuk mengoperasikan mesin dengan tekanan kilat tinggi disediakan oleh rangkaian daya mesin dengan baut baja pendukung, blok aluminium cor yang diturunkan dari aksi gaya gas, dan tidak adanya sambungan gas. Meningkatkan proses pembersihan dan pengisian silinder (dan ini merupakan masalah untuk semua mesin diesel 2-tak) difasilitasi sampai batas tertentu oleh skema gas-dinamis menggunakan energi kinetik dari gas buang dan efek ejeksi.
Sistem pembentukan campuran jet-vortex, di mana sifat dan arah jet bahan bakar dikoordinasikan dengan arah pergerakan udara, memastikan turbulisasi efektif campuran bahan bakar-udara, yang berkontribusi pada peningkatan proses perpindahan panas dan massa.
Bentuk ruang bakar yang dipilih secara khusus juga memungkinkan untuk meningkatkan proses pencampuran dan pembakaran. Tutup bantalan utama ditarik bersama dengan bak mesin oleh baut daya baja, mengambil beban dari gaya gas yang bekerja pada piston.
Sebuah pelat dengan turbin dan pompa air dipasang di salah satu ujung blok bak mesin, dan pelat transmisi utama dan penutup dengan penggerak ke supercharger, regulator, sensor tachometer, kompresor tekanan tinggi, dan distributor udara dipasang di seberangnya. akhir.
Pada Januari 1957, prototipe pertama mesin diesel tangki 5TD disiapkan untuk tes bangku. Pada akhir tes bangku, 5TD pada tahun yang sama dipindahkan untuk uji coba objek (laut) di tangki eksperimental "Objek 430", dan pada Mei 1958 lulus tes antardepartemen dengan nilai bagus.
Namun demikian, diputuskan untuk tidak mentransfer diesel 5TD ke produksi massal. Alasannya lagi-lagi perubahan persyaratan militer untuk tank baru, yang sekali lagi mengharuskan peningkatan kekuatan. Mempertimbangkan indikator teknis dan ekonomi yang sangat tinggi dari mesin 5TD dan cadangan yang melekat di dalamnya (yang juga ditunjukkan oleh tes), pembangkit listrik baru dengan kapasitas sekitar 700 hp. memutuskan untuk membuat atas dasar.
Penciptaan mesin asli untuk pabrik teknik transportasi Kharkov membutuhkan pembuatan peralatan teknologi yang signifikan, sejumlah besar prototipe mesin diesel dan pengujian berulang jangka panjang. Harus diingat bahwa departemen desain pabrik kemudian menjadi Biro Desain Teknik Mesin Kharkov (KHKBD), dan produksi motor dibuat praktis dari awal setelah perang.
Bersamaan dengan desain mesin diesel, kompleks besar tempat percobaan dan berbagai instalasi (24 unit) dibuat di pabrik untuk menguji elemen desain dan alur kerjanya. Ini sangat membantu untuk memeriksa dan mengerjakan desain unit seperti supercharger, turbin, pompa bahan bakar, manifold buang, centrifuge, pompa air dan minyak, bak mesin blok, dll., namun, pengembangannya berlanjut lebih jauh.
Pada tahun 1959, atas permintaan kepala perancang tangki baru (AA Morozov), untuk siapa mesin diesel ini dirancang untuk tujuan itu, dianggap perlu untuk meningkatkan dayanya dari 426 kW (580 hp) menjadi 515 kW (700 hp). hp).). Versi paksa mesin diberi nama 5TDF.
Dengan meningkatkan kecepatan kompresor boost, daya liter mesin meningkat. Namun, akibat pemaksaan mesin diesel, masalah baru muncul, terutama pada keandalan komponen dan rakitan.
Perancang KhKBD, NIID, VNIITransmash, teknologi pabrik dan institut VNITI dan TsNITI (sejak 1965) telah melakukan sejumlah besar perhitungan, penelitian, desain, dan pekerjaan teknologi untuk mencapai keandalan dan waktu pengoperasian mesin diesel 5TDF yang diperlukan.
Masalah yang paling sulit ternyata adalah masalah peningkatan kehandalan kelompok piston, peralatan bahan bakar, dan turbocharger. Setiap, bahkan yang tidak signifikan, peningkatan diberikan hanya sebagai hasil dari seluruh rangkaian ukuran desain, teknologi, organisasi (produksi).
Batch pertama mesin diesel 5TDF ditandai dengan ketidakstabilan besar dalam kualitas suku cadang dan rakitan. Bagian tertentu dari mesin diesel dari seri yang diproduksi (batch) telah mengumpulkan waktu operasi garansi yang ditetapkan (300 jam). Pada saat yang sama, sebagian besar mesin dilepas dari dudukannya sebelum waktu operasi garansi karena cacat tertentu.
Kekhasan mesin diesel 2-tak berkecepatan tinggi terletak pada sistem pertukaran gas yang lebih kompleks daripada 4-tak, peningkatan konsumsi udara, dan beban panas yang lebih tinggi dari grup piston. Oleh karena itu, kekakuan dan ketahanan getaran dari struktur, kepatuhan yang lebih ketat terhadap bentuk geometris dari sejumlah bagian, sifat anti-rebut yang tinggi dan ketahanan aus silinder, ketahanan panas dan kekuatan mekanis piston, pasokan dan pelepasan pelumas silinder dengan hati-hati dan peningkatan kualitas permukaan gosok diperlukan. Untuk mempertimbangkan fitur-fitur khusus dari mesin 2-tak ini, perlu untuk memecahkan masalah desain dan teknologi yang kompleks.
Salah satu bagian paling penting yang menyediakan distribusi gas yang tepat dan perlindungan cincin penyegel piston dari panas berlebih adalah cincin api tipe manset baja berdinding tipis dengan lapisan anti-gesekan khusus. Dalam penyempurnaan mesin diesel 5TDF, masalah pengoperasian cincin ini menjadi salah satu yang utama. Dalam proses fine-tuning, untuk waktu yang lama, lecet dan kerusakan cincin api terjadi karena deformasi bidang pendukungnya, konfigurasi suboptimal dari cincin itu sendiri dan badan piston, pelapisan krom cincin yang tidak memuaskan, pelumasan yang tidak mencukupi., pasokan bahan bakar yang tidak merata oleh nozel, serpihan kerak dan pengendapan garam yang terbentuk pada lapisan piston, serta karena keausan debu yang terkait dengan tingkat pembersihan yang tidak memadai dari udara yang ditarik oleh mesin.
Hanya sebagai hasil kerja panjang dan kerja keras dari banyak spesialis pabrik dan lembaga penelitian dan teknologi, ketika konfigurasi piston dan cincin api ditingkatkan, teknologi manufaktur ditingkatkan, elemen-elemen peralatan bahan bakar ditingkatkan, pelumasan ditingkatkan, penggunaan lapisan anti-gesekan yang lebih efektif, serta penyempurnaan cacat sistem pembersihan udara yang terkait dengan pengoperasian cincin api praktis dihilangkan.
Kerusakan cincin piston trapesium, misalnya, dihilangkan dengan mengurangi jarak aksial antara cincin dan alur piston, meningkatkan material, mengubah konfigurasi penampang cincin (beralih dari trapesium ke persegi panjang) dan menyempurnakan teknologi untuk pembuatan cincin. Fraktur baut liner piston telah diperbaiki dengan memasang kembali dan mengunci, mengencangkan kontrol manufaktur, mengencangkan batas torsi, dan menggunakan bahan baut yang ditingkatkan.
Stabilitas konsumsi oli dicapai dengan meningkatkan kekakuan silinder, mengurangi ukuran potongan di ujung silinder, mengencangkan kontrol dalam pembuatan cincin pengumpul oli.
Dengan menyempurnakan elemen peralatan bahan bakar dan meningkatkan pertukaran gas, beberapa peningkatan efisiensi bahan bakar dan penurunan tekanan flash maksimum diperoleh.
Dengan meningkatkan kualitas karet yang digunakan dan merampingkan celah antara silinder dan blok, kasus kebocoran cairan pendingin melalui cincin penyegel karet dihilangkan.
Sehubungan dengan peningkatan yang signifikan dalam rasio roda gigi dari poros engkol ke supercharger, beberapa mesin diesel 5TDF mengungkapkan cacat seperti tergelincir dan keausan pada cakram kopling gesekan, kerusakan roda supercharger dan kegagalan bantalannya, yang tidak ada pada mesin diesel 5TD. Untuk menghilangkannya, perlu dilakukan tindakan seperti memilih pengencangan optimal dari paket cakram kopling gesekan, menambah jumlah cakram dalam paket, menghilangkan konsentrator tegangan pada impeller supercharger, menggetarkan roda, meningkatkan sifat redaman dari dukungan, dan memilih bantalan yang lebih baik. Hal ini memungkinkan untuk menghilangkan cacat akibat memaksa mesin diesel dalam hal tenaga.
Peningkatan keandalan dan waktu pengoperasian mesin diesel 5TDF sebagian besar berkontribusi pada penggunaan oli berkualitas lebih tinggi dengan aditif khusus.
Di tribun VNIITransmash, dengan partisipasi karyawan KKBD dan NIID, sejumlah besar penelitian dilakukan pada pengoperasian mesin diesel 5TDF dalam kondisi debu nyata dari udara masuk. Mereka akhirnya mencapai puncaknya dalam uji "debu" mesin yang berhasil selama 500 jam operasi. Ini menegaskan tingkat pengembangan yang tinggi dari kelompok silinder-piston dari mesin diesel dan sistem pembersihan udara.
Sejalan dengan fine-tuning diesel itu sendiri, itu berulang kali diuji dalam hubungannya dengan sistem pembangkit listrik. Pada saat yang sama, sistem sedang diperbaiki, masalah interkoneksi dan operasi yang andal di dalam tangki sedang diselesaikan.
L. L. Golinets adalah kepala desainer KHKBD pada periode yang menentukan untuk menyempurnakan mesin diesel 5TDF. Mantan kepala desainer A. D. Charomsky telah pensiun dan terus mengambil bagian dalam penyempurnaan sebagai konsultan.
Pengembangan produksi serial mesin diesel 5TDF di bengkel pabrik baru yang dibangun khusus, dengan kader pekerja dan insinyur baru yang mempelajari mesin ini, menyebabkan banyak kesulitan, partisipasi spesialis dari organisasi lain.
Hingga tahun 1965, mesin 5TDF diproduksi dalam seri terpisah (lot). Setiap seri berikutnya mencakup sejumlah tindakan yang dikembangkan dan diuji di tribun, menghilangkan cacat yang diidentifikasi selama pengujian dan selama operasi uji coba di ketentaraan.
Namun, waktu pengoperasian mesin yang sebenarnya tidak melebihi 100 jam.
Terobosan signifikan dalam meningkatkan keandalan mesin diesel terjadi pada awal tahun 1965. Pada saat ini, sejumlah besar perubahan telah dilakukan pada desain dan teknologi pembuatannya. Diperkenalkan ke dalam produksi, perubahan ini memungkinkan untuk meningkatkan waktu pengoperasian seri mesin berikutnya hingga 300 jam. Pengujian tangki jangka panjang dengan mesin seri ini mengkonfirmasi peningkatan keandalan mesin diesel yang signifikan: semua mesin selama pengujian ini bekerja 300 jam, dan beberapa di antaranya (secara selektif), melanjutkan pengujian, bekerja masing-masing 400 … 500 jam.
Pada tahun 1965, batch instalasi mesin diesel akhirnya dirilis sesuai dengan dokumentasi gambar teknis yang dikoreksi dan teknologi untuk produksi massal. Sebanyak 200 mesin seri diproduksi pada tahun 1965. Peningkatan produksi dimulai, mencapai puncaknya pada tahun 1980. Pada bulan September 1966, mesin diesel 5TDF lulus uji antardepartemen.
Mengingat sejarah penciptaan mesin diesel 5TDF, perlu dicatat kemajuan perkembangan teknologinya sebagai mesin yang benar-benar baru untuk produksi pabrik. Hampir bersamaan dengan pembuatan prototipe mesin dan penyempurnaan desainnya, pengembangan teknologinya dan pembangunan fasilitas produksi baru pabrik dan penyelesaiannya dengan peralatan dilakukan.
Menurut gambar yang direvisi dari sampel mesin pertama, sudah pada tahun 1960, pengembangan teknologi desain untuk pembuatan 5TDF dimulai, dan pada tahun 1961, produksi dokumentasi teknologi kerja dimulai. Fitur desain mesin diesel 2-tak, penggunaan material baru, akurasi tinggi dari individu dan komponennya memerlukan teknologi untuk menggunakan metode baru yang mendasar dalam memproses dan bahkan merakit mesin. Desain proses teknologi dan peralatannya dilakukan baik oleh layanan teknologi pabrik, yang dipimpin oleh A. I. Isaev, V. D. Dyachenko, V. I. Doschechkin dan lainnya, dan oleh karyawan institut teknologi industri. Spesialis dari Central Research Institute of Materials (direktur F. A. Kupriyanov) terlibat dalam memecahkan banyak masalah ilmu metalurgi dan material.
Pembangunan bengkel baru untuk produksi motor Pabrik Teknik Transportasi Kharkov dilakukan sesuai dengan proyek Institut Soyuzmashproekt (kepala insinyur proyek S. I. Shpynov).
Selama tahun 1964-1967. produksi diesel baru selesai dengan peralatan (terutama mesin khusus - lebih dari 100 unit), yang tanpanya hampir tidak mungkin untuk mengatur produksi serial suku cadang diesel. Ini adalah mesin bor berlian dan multi-spindel untuk pemrosesan blok, mesin pembubutan dan penyelesaian khusus untuk pemrosesan poros engkol, dll. Sebelum commissioning bengkel baru dan area pengujian dan debugging teknologi manufaktur untuk sejumlah bagian utama, serta pembuatan batch instalasi dan seri pertama mesin, lambung lokomotif diesel besar untuk sementara diatur di produksi. situs.
Pengoperasian kapasitas utama produksi diesel baru dilakukan secara bergantian pada periode 1964-1967. Di bengkel baru, siklus penuh produksi diesel 5TDF disediakan, kecuali untuk produksi kosong yang terletak di lokasi utama pabrik.
Ketika membentuk fasilitas produksi baru, banyak perhatian diberikan pada peningkatan level dan organisasi produksi. Produksi mesin diesel diatur menurut prinsip garis dan kelompok, dengan mempertimbangkan pencapaian terakhir periode itu di bidang ini. Cara mekanisasi dan otomatisasi pemrosesan dan perakitan suku cadang yang paling canggih digunakan, yang memastikan terciptanya produksi mekanis mesin diesel 5TDF yang komprehensif.
Dalam proses pembentukan produksi, kerja bersama besar antara teknolog dan desainer dilakukan untuk meningkatkan kemampuan manufaktur desain mesin diesel, di mana para teknolog mengeluarkan sekitar enam ribu proposal ke KHKBD, sebagian besar di antaranya tercermin dalam dokumentasi desain mesin.
Dari segi teknis, produksi solar baru secara signifikan melebihi indikator perusahaan industri yang menghasilkan produk serupa yang dicapai pada saat itu. Faktor peralatan dari proses produksi diesel 5TDF telah mencapai nilai tinggi - 6, 22. Hanya dalam 3 tahun, lebih dari 10 ribu proses teknologi telah dikembangkan, lebih dari 50 ribu item peralatan telah dirancang dan diproduksi. Sejumlah perusahaan Dewan Ekonomi Kharkov terlibat dalam pembuatan peralatan dan peralatan, untuk membantu pabrik Malyshev.
Pada tahun-tahun berikutnya (setelah 1965), sudah dalam proses produksi serial mesin diesel 5TDF, layanan teknologi pabrik dan TsNITI melakukan pekerjaan untuk lebih meningkatkan teknologi untuk mengurangi intensitas tenaga kerja, meningkatkan kualitas dan keandalan mesin. mesin. Karyawan TsNITI (direktur Ya. A. Shifrin, chief engineer B. N. Surnin) selama 1967-1970. lebih dari 4500 proposal teknologi telah dikembangkan, memberikan pengurangan intensitas tenaga kerja lebih dari 530 jam standar dan pengurangan yang signifikan dalam kerugian dari skrap selama produksi. Pada saat yang sama, langkah-langkah ini memungkinkan untuk mengurangi lebih dari separuh jumlah operasi pemasangan dan penyambungan bagian secara selektif. Hasil dari penerapan langkah-langkah desain dan teknologi yang kompleks adalah pengoperasian mesin yang lebih andal dan berkualitas tinggi dengan waktu pengoperasian yang dijamin 300 jam. Tetapi pekerjaan para ahli teknologi pabrik dan TsNITI, bersama dengan perancang KHKBD, terus berlanjut. Itu perlu untuk meningkatkan waktu pengoperasian mesin 5TDF sebesar 1,5 … 2,0 kali. Tugas ini juga diselesaikan. Mesin diesel tangki 2-tak 5TDF dimodifikasi dan mulai diproduksi di Pabrik Teknik Transportasi Kharkov.
Peran yang sangat signifikan dalam mengatur produksi diesel 5TDF dimainkan oleh direktur pabrik O. A. Soich, serta sejumlah pemimpin industri (D. F. Ustinov, E. P. Shkurko, I. F. Dmitriev, dll.), terus memantau kemajuan dan perkembangan produksi diesel, serta mereka yang terlibat langsung dalam memecahkan masalah teknis dan organisasi.
Pemanasan suar otomatis dan sistem injeksi oli memungkinkan untuk pertama kalinya (pada 1978) untuk memberikan start dingin mesin diesel tangki pada suhu hingga -20 derajat C (dari 1984 hingga -25 derajat C). Kemudian (pada tahun 1985) menjadi mungkin dengan bantuan sistem PVV (pemanas udara masuk) untuk melakukan start dingin mesin diesel empat langkah (V-84-1) pada tangki T-72, tetapi hanya hingga suhu -20 derajat C, dan tidak lebih dari dua puluh dimulai dalam sumber daya garansi.
Yang terpenting, 5TDF telah bertransisi dengan mulus ke kualitas baru pada mesin diesel seri 6TD (6TD-1… 6TD-4) dengan rentang daya 1000-1500 hp.dan melampaui analog asing dalam sejumlah parameter dasar.
INFORMASI PENGOPERASIAN MESIN
Bahan operasi terapan
Jenis bahan bakar utama untuk menyalakan mesin adalah bahan bakar untuk mesin diesel berkecepatan tinggi GOST 4749-73:
pada suhu sekitar tidak lebih rendah dari + 5 ° - merek DL;
pada suhu sekitar dari +5 hingga -30 ° - merek DZ;
pada suhu sekitar di bawah -30 ° - merek DA.
Jika perlu, diperbolehkan menggunakan bahan bakar DZ pada suhu sekitar di atas + 50 ° C.
Selain bahan bakar untuk mesin diesel berkecepatan tinggi, mesin dapat beroperasi dengan bahan bakar jet TC-1 GOST 10227-62 atau motor bensin A-72 GOST 2084-67, serta campuran bahan bakar yang digunakan dalam proporsi apa pun.
Oli M16-IHP-3 TU 001226-75 digunakan untuk pelumasan mesin. Dengan tidak adanya oli ini, penggunaan oli MT-16p diperbolehkan.
Saat mengganti oli satu ke oli lainnya, oli sisa dari bak mesin dan tangki oli mesin harus dikuras.
Dilarang mencampur minyak yang digunakan satu sama lain, serta penggunaan minyak merek lain. Diperbolehkan untuk mencampur dalam sistem oli residu yang tidak mengering dari satu merek oli dengan yang lain, diisi ulang.
Saat menguras, suhu oli tidak boleh lebih rendah dari + 40 ° C.
Untuk mendinginkan mesin pada suhu sekitar minimal + 5 ° C, air tawar murni tanpa kotoran mekanis digunakan, melewati filter khusus yang dipasok ke EC mesin.
Untuk melindungi mesin dari korosi dan pembentukan acipe, 0,15% aditif tiga komponen (0,05% dari setiap komponen) ditambahkan ke air yang melewati filter.
Aditif terdiri dari trisodium phosphate GOST 201-58, puncak kalium kromium GOST 2652-71 dan natrium nitrit GOST 6194-69 pertama-tama harus dilarutkan dalam 5-6 liter air yang melewati filter kimia dan dipanaskan hingga suhu 60-80 ° C Dalam hal pengisian bahan bakar 2-3 liter, diperbolehkan (satu kali) menggunakan air tanpa aditif.
Jangan menuangkan aditif anti korosi langsung ke dalam sistem.
Dengan tidak adanya aditif tiga komponen, diizinkan untuk menggunakan puncak kromium murni 0,5%.
Pada suhu sekitar di bawah + 50 ° C, cairan beku rendah (antibeku) "40" atau "65" GOST 159-52 harus digunakan. Antibeku merek "40" digunakan pada suhu sekitar hingga -35 ° C, pada suhu di bawah -35 ° C - merek antibeku "65".
Isi mesin dengan bahan bakar, oli, dan cairan pendingin sesuai dengan langkah-langkah untuk mencegah masuknya kotoran dan debu mekanis, serta kelembapan ke dalam bahan bakar dan oli.
Disarankan untuk mengisi bahan bakar dengan bantuan tanker khusus atau perangkat pengisian bahan bakar biasa (saat mengisi bahan bakar dari wadah terpisah).
Bahan bakar harus diisi ulang melalui filter sutra. Disarankan untuk mengisi oli dengan bantuan pengisi oli khusus. Isi minyak, air, dan cairan dengan titik beku rendah melalui filter dengan mesh No. 0224 GOST 6613-53.
Isi sistem ke tingkat yang ditentukan dalam instruksi pengoperasian mesin.
Untuk benar-benar mengisi volume sistem pelumasan dan pendinginan, setelah mengisi bahan bakar, nyalakan mesin selama 1-2 menit, lalu periksa levelnya dan, jika perlu, isi bahan bakar sistem, Selama operasi, perlu untuk mengontrol jumlah cairan pendingin dan oli dalam sistem engine dan mempertahankan level IB mereka dalam batas yang ditentukan.
Jangan biarkan mesin hidup jika ada kurang dari 20 liter oli di tangki pelumasan mesin.
Jika level cairan pendingin turun karena penguapan atau kebocoran ke dalam sistem pendingin, tambahkan air atau antibeku, masing-masing.
Kuras cairan pendingin dan oli melalui katup pembuangan khusus mesin dan mesin (ketel pemanas dan tangki oli) menggunakan selang dengan fitting dengan bukaan pengisi terbuka. Untuk benar-benar menghilangkan sisa air dari sistem pendingin untuk menghindari pembekuan, disarankan untuk menumpahkan sistem dengan 5-6 liter cairan dengan titik beku rendah.
Fitur pengoperasian mesin pada berbagai jenis bahan bakar
Pengoperasian mesin pada berbagai jenis bahan bakar dilakukan oleh mekanisme kontrol umpan bahan bakar yang memiliki dua posisi untuk mengatur tuas multi-bahan bakar: pengoperasian bahan bakar untuk mesin diesel kecepatan tinggi, bahan bakar untuk mesin jet, bensin (dengan penurunan daya) dan campurannya dalam proporsi apa pun; bekerja hanya pada bensin.
Pengoperasian pada jenis bahan bakar lain dengan posisi tuas ini sangat dilarang.
Pemasangan mekanisme kontrol pengumpanan bahan bakar dari posisi "Operation on solar" ke posisi "Operation on gasoline" dilakukan dengan memutar sekrup penyetel tuas multi-fuel searah jarum jam hingga berhenti, dan dari posisi "Operation on bensin" ke posisi "Operasi pada bahan bakar diesel" - dengan memutar sekrup penyetel tuas multi-bahan bakar berlawanan arah jarum jam hingga berhenti.
Fitur memulai dan mengoperasikan mesin saat menggunakan bensin. Setidaknya 2 menit sebelum menghidupkan mesin, perlu menyalakan pompa BCN mesin dan memompa bahan bakar secara intensif dengan pompa priming manual mesin; dalam semua kasus, terlepas dari suhu sekitar, sebelum memulai, injeksikan oli dua kali ke dalam silinder.
Pompa sentrifugal bensin mesin harus tetap hidup selama mesin berjalan dengan bensin, campurannya dengan bahan bakar lain, dan selama mesin berhenti sebentar (3-5 menit).
Kecepatan idle stabil minimum saat mesin berjalan dengan bensin adalah 1000 per menit.
FITUR OPERASI
S. Suvorov mengingat kelebihan dan kekurangan mesin ini dalam bukunya "T-64".
Pada tank T-64A, yang diproduksi sejak 1975, pelindung turret juga diperkuat karena penggunaan pengisi korundum.
Pada mesin-mesin ini, kapasitas tangki bahan bakar juga ditingkatkan dari 1093 liter menjadi 1270 liter, sebagai akibatnya sebuah kotak untuk menyimpan suku cadang muncul di bagian belakang menara. Pada mesin rilis sebelumnya, suku cadang dan aksesori ditempatkan dalam kotak di spatbor kanan, di mana tangki bahan bakar tambahan dipasang, terhubung ke sistem bahan bakar. Ketika pengemudi memasang katup distribusi bahan bakar pada kelompok tangki mana pun (belakang atau depan), bahan bakar diproduksi terutama dari tangki eksternal.
Sepasang worm-gear digunakan dalam mekanisme pengencangan track, yang memungkinkan pengoperasiannya tanpa perawatan selama seluruh masa pakai tangki.
Karakteristik kinerja mesin ini telah sangat ditingkatkan. Jadi, misalnya, uji coba sebelum layanan nomor berikutnya ditingkatkan dari 1500 dan 3000 km menjadi 2500 dan 5000 km untuk T01 dan TO, masing-masing. Sebagai perbandingan, pada tangki T-62 TO1 TO2 dilakukan setelah lari 1000 dan 2000 km, dan pada tangki T-72 - masing-masing setelah lari 1600-1800 dan 3300-3500 km. Masa garansi untuk mesin 5TDF ditingkatkan dari 250 menjadi 500 jam, masa garansi untuk seluruh alat berat adalah 5.000 km.
Tapi sekolah itu hanya pendahuluan, operasi utama dimulai di pasukan, di mana saya berakhir setelah lulus dari perguruan tinggi pada tahun 1978. Tepat sebelum kelulusan, kami diberitahu tentang perintah Panglima Angkatan Darat bahwa lulusan sekolah kami harus didistribusikan hanya ke formasi di mana ada tank T-64. Ini disebabkan oleh fakta bahwa di pasukan ada kasus kegagalan massal tank T-64, khususnya mesin 5TDF. Alasannya - ketidaktahuan tentang bahan dan aturan pengoperasian tangki ini. Adopsi tangki T-64 sebanding dengan transisi dalam penerbangan dari mesin piston ke mesin jet - veteran penerbangan ingat bagaimana itu.
Adapun mesin 5TDF, ada dua alasan utama kegagalannya pada pasukan - panas berlebih dan keausan debu. Kedua alasan itu karena ketidaktahuan atau pengabaian aturan operasi. Kelemahan utama dari mesin ini adalah tidak terlalu dirancang untuk orang bodoh, terkadang mengharuskan mereka melakukan apa yang tertulis dalam petunjuk pengoperasian. Ketika saya sudah menjadi komandan kompi tank, salah satu komandan peleton saya, lulusan Sekolah Tank Chelyabinsk, yang melatih perwira untuk tank T-72, entah bagaimana mulai mengkritik pembangkit listrik tank T-64. Dia tidak menyukai mesin dan frekuensi perawatannya. Tetapi ketika dia ditanya pertanyaan "Berapa kali dalam enam bulan Anda membuka atap MTO di tiga tangki pelatihan Anda dan melihat ke kompartemen transmisi mesin?" Ternyata tidak pernah. Dan tank-tank itu pergi, memberikan pelatihan tempur.
Dan seterusnya secara berurutan. Overheating mesin terjadi karena beberapa alasan. Pertama, mekanik lupa melepas tikar dari radiator dan kemudian tidak melihat instrumen, tetapi ini sangat jarang terjadi dan, sebagai suatu peraturan, di musim dingin. Yang kedua dan utama adalah mengisi dengan cairan pendingin. Menurut instruksi, itu seharusnya mengisi air (selama periode operasi musim panas) dengan aditif tiga komponen, dan air harus diisi melalui sulfofilter khusus, yang dengannya semua mesin rilis awal dilengkapi, dan pada yang baru mesin satu filter tersebut dikeluarkan per perusahaan (10-13 tangki). Mesin gagal, terutama tank dari kelompok operasi pelatihan, yang dioperasikan setidaknya lima hari seminggu dan biasanya terletak di kisaran di taman lapangan. Pada saat yang sama, "buku teks" mekanik pengemudi (yang disebut mekanik mesin pelatihan), sebagai aturan, pekerja keras dan orang-orang yang teliti, tetapi tidak tahu seluk-beluk mesin, kadang-kadang mampu menuangkan air ke dalam sistem pendingin hanya dari keran, terutama karena sulfofilter (yang satu per perusahaan) biasanya disimpan di tempat musim dingin, di suatu tempat di loker chief technical officer perusahaan. Hasilnya adalah pembentukan kerak di saluran tipis sistem pendingin (di area ruang bakar), kurangnya sirkulasi cairan di bagian mesin yang paling panas, panas berlebih dan kegagalan mesin. Pembentukan kerak diperparah oleh fakta bahwa air di Jerman sangat keras.
Begitu berada di unit tetangga, mesin dilepas karena terlalu panas karena kesalahan pengemudi. Setelah menemukan kebocoran kecil pendingin dari radiator, atas saran salah satu "ahli" untuk menambahkan mustard ke sistem, ia membeli sebungkus mustard di toko dan menuangkan semuanya ke dalam sistem, akibatnya - penyumbatan saluran dan kegagalan mesin.
Ada juga kejutan lain dengan sistem pendingin. Tiba-tiba, ia mulai mengeluarkan cairan pendingin dari sistem pendingin melalui katup uap-udara (PVK). Beberapa, tidak mengerti apa masalahnya, mencoba memulainya dari tarikan - hasil dari kerusakan mesin. Jadi, wakil kepala batalion saya membuatkan saya "hadiah" untuk Tahun Baru, dan saya harus mengganti mesin pada tanggal 31 Desember. Saya punya waktu sebelum Tahun Baru, karena mengganti mesin pada tangki T-64 bukanlah prosedur yang sangat rumit dan, yang paling penting, tidak memerlukan penyelarasan saat memasangnya. Sebagian besar waktu ketika mengganti mesin pada tangki T-64, seperti pada semua tangki domestik, dilakukan dengan prosedur pengurasan dan pengisian bahan bakar minyak dan cairan pendingin. Jika tangki kami memiliki konektor dengan katup, bukan sambungan duri, seperti pada Leopard atau Leclercs, maka mengganti mesin pada tangki T-64 atau T-80 pada waktunya tidak lebih dari mengganti seluruh unit daya di tangki barat. Misalnya, pada hari yang tak terlupakan itu, 31 Desember 1980, setelah menguras oli dan cairan pendingin, Warrant Officer E. Sokolov dan saya "melempar" mesin keluar dari MTO hanya dalam waktu 15 menit.
Alasan kedua untuk kegagalan mesin 5TDF adalah keausan debu. Sistem pemurnian udara. Jika Anda tidak memeriksa level cairan pendingin secara tepat waktu, tetapi harus diperiksa sebelum setiap keluar dari mesin, maka akan tiba saatnya ketika tidak akan ada cairan di bagian atas jaket pendingin, dan terjadi panas berlebih lokal. Dalam hal ini, titik terlemah adalah nosel. Dalam hal ini, gasket injektor terbakar atau injektor itu sendiri gagal, kemudian melalui celah di dalamnya atau gasket yang terbakar, gas dari silinder menerobos ke sistem pendingin, dan di bawah tekanannya cairan dikeluarkan melalui PVCL. Semua ini tidak fatal bagi mesin dan dihilangkan jika ada orang yang berpengetahuan luas di unit. Pada mesin in-line dan berbentuk V konvensional dalam situasi yang sama, "mengarah" paking kepala silinder, dan dalam hal ini akan ada lebih banyak pekerjaan.
Jika dalam situasi seperti itu mesin dihentikan dan tidak ada tindakan yang diambil, maka setelah beberapa saat silinder akan mulai diisi dengan cairan pendingin, mesin adalah kisi inersia dan pembersih udara siklon. Pembersih udara, menurut petunjuk pengoperasian, dibilas sesuai kebutuhan. Pada tangki tipe T-62, itu dicuci di musim dingin setelah 1000 km, dan di musim panas setelah 500 km. Pada tangki T-64 - sesuai kebutuhan. Di sinilah batu sandungan masuk - beberapa menganggapnya sebagai fakta bahwa Anda tidak perlu mencucinya sama sekali. Kebutuhan muncul ketika minyak masuk ke dalam angin topan. Dan jika setidaknya salah satu dari 144 siklon mengandung minyak, maka pembersih udara harus disiram, karena melalui siklon ini, udara kotor dengan debu masuk ke mesin, dan kemudian, seperti ampelas, liner silinder dan ring piston terhapus. Mesin mulai kehilangan tenaga, konsumsi oli meningkat, dan kemudian berhenti sama sekali.
Tidak sulit untuk memeriksa masuknya minyak ke dalam siklon - lihat saja saluran masuk siklon di pembersih udara. Biasanya mereka melihat pipa pembuangan debu dari pembersih udara, dan jika ada minyak di atasnya, maka mereka melihat pembersih udara, dan jika perlu, mencucinya. Dari mana minyak itu berasal? Sederhana saja: leher pengisi tangki oli dari sistem pelumasan mesin terletak di sebelah saluran masuk udara. Saat mengisi bahan bakar dengan minyak, kaleng penyiram biasanya digunakan, tetapi karena lagi, pada mesin pelatihan, kaleng penyiraman, sebagai suatu peraturan, tidak ada (seseorang hilang, seseorang meletakkannya di sabuk ulat, lupa dan melewatinya, dll.), Kemudian mekanik hanya menuangkan minyak dari ember, sementara minyak tumpah, pertama jatuh di jaring asupan udara, dan kemudian ke pembersih udara. Bahkan ketika mengisi minyak melalui kaleng penyiram, tetapi dalam cuaca berangin, angin memercikkan minyak ke jaring pembersih udara. Oleh karena itu, ketika mengisi bahan bakar minyak, saya meminta bawahan saya untuk memasang alas dari suku cadang dan aksesori tangki pada saluran masuk udara, sebagai akibatnya saya menghindari masalah dengan keausan debu pada mesin. Perlu dicatat bahwa kondisi berdebu di Jerman pada musim panas adalah yang paling parah. Jadi, misalnya, selama latihan divisi pada bulan Agustus 1982, ketika melakukan pawai melalui pembukaan hutan Jerman, karena debu yang menggantung, bahkan tidak terlihat di mana laras meriam tanknya sendiri berakhir. Jarak antara mobil-mobil di kolom dijaga secara harfiah oleh aroma. Ketika ada beberapa meter tersisa untuk tangki terkemuka, adalah mungkin untuk membedakan bau gas buang dan rem tepat waktu. Dan 150 kilometer. Setelah pawai, semuanya: tank, orang dan wajah mereka, overall dan sepatu bot memiliki warna yang sama - warna debu jalan.
Diesel 6TD
Bersamaan dengan desain dan penyempurnaan teknologi mesin diesel 5TDF, tim desain KKBD mulai mengembangkan model berikutnya dari mesin diesel 2-tak yang sudah dalam desain 6 silinder dengan peningkatan daya hingga 735 kW (1000 hp). Mesin ini, seperti 5TDF, adalah mesin diesel dengan silinder yang disusun secara horizontal, piston yang bergerak berlawanan, dan hembusan aliran langsung. Diesel itu bernama 6TD.
Turbocharging dilakukan dari kompresor secara mekanis (pegas) yang terhubung ke turbin gas, mengubah sebagian energi panas dari gas buang menjadi kerja mekanis untuk menggerakkan kompresor.
Karena daya yang dikembangkan oleh turbin tidak cukup untuk menggerakkan kompresor, ia terhubung ke kedua poros engkol mesin menggunakan gearbox dan mekanisme transmisi. Rasio kompresi diambil menjadi 15.
Untuk mendapatkan timing katup yang diperlukan, di mana pembersihan silinder yang diperlukan dari gas buang dan pengisian dengan udara terkompresi akan disediakan, perpindahan sudut poros engkol disediakan (seperti pada mesin 5TDF) dalam kombinasi dengan pengaturan asupan yang asimetris. dan lubang pembuangan silinder sepanjang panjangnya. Torsi yang diambil dari poros engkol adalah 30% untuk poros masuk dan 70% untuk buang dari torsi mesin. Torsi yang dikembangkan pada poros masuk ditransmisikan melalui transmisi roda gigi ke poros buang. Torsi total dapat diambil dari kedua ujung poros buang melalui kopling lepas landas daya.
Pada bulan Oktober 1979, mesin 6TD, setelah revisi serius dari kelompok silinder-piston, peralatan bahan bakar, sistem pasokan udara, dan elemen lainnya, berhasil lulus uji antardepartemen. Sejak 1986, mesin seri 55 pertama telah diproduksi. Pada tahun-tahun berikutnya, produksi serial meningkat dan mencapai puncaknya pada tahun 1989.
Persentase penyatuan bagian demi bagian 6TD dengan mesin diesel 5TDF lebih dari 76%, dan keandalan operasi tidak lebih rendah dari 5TDF, yang telah diproduksi secara massal selama bertahun-tahun.
Pekerjaan KHKBD di bawah kepemimpinan kepala desainer N. K. Ryazantsev untuk lebih meningkatkan mesin diesel tangki 2-tak berlanjut. Unit, mekanisme dan sistem sedang diselesaikan, yang dengannya cacat individu diidentifikasi dalam operasi. Sistem tekanan ditingkatkan. Banyak tes bangku mesin dilakukan dengan diperkenalkannya perubahan desain.
Sebuah modifikasi baru dari mesin diesel, 6TD-2, sedang dikembangkan. Tenaganya tidak lagi 735 kW (1000 hp), seperti pada 6TD, tetapi 882 kW (1200 hp). Penyatuan terperincinya dengan mesin diesel 6TD disediakan oleh lebih dari 90%, dan dengan mesin diesel 5TDF - lebih dari 69%.
Berbeda dengan mesin 6TD, mesin 6TD-2 menggunakan kompresor sentrifugal aksial 2 tahap dari sistem tekanan dan perubahan desain turbin, bellow, filter oli sentrifugal, pipa cabang, dan unit lainnya. Rasio kompresi juga sedikit berkurang - dari 15 menjadi 14,5 dan tekanan efektif rata-rata meningkat dari 0,98 MPa menjadi 1,27 MPa. Konsumsi bahan bakar spesifik mesin 6TD-2 adalah 220 g / (kW * h) (162 g / (hp * h)) bukannya 215 g / (kW * h) (158 g / (hp * h)) - untuk 6TD. Dari sudut pandang pemasangan di tangki, mesin diesel 6TD-2 benar-benar dapat dipertukarkan dengan mesin 6DT.
Pada tahun 1985 Diesel 6TD-2 lulus tes antar departemen dan dokumentasi desain diserahkan untuk persiapan dan organisasi produksi serial.
Di KKBD, dengan partisipasi NIID dan organisasi lain, penelitian dan pengembangan mesin diesel 2-tak 6TD dilanjutkan dengan tujuan meningkatkan kekuatannya menjadi 1103 kW (1500hp), 1176 kW (1600hp), 1323 kW (1800hp) dengan pengujian pada sampel, serta menciptakan atas dasar keluarga mesin untuk VGM dan mesin ekonomi nasional. Untuk VGM kategori ringan dan menengah, mesin diesel 3TD dengan kapasitas 184 … 235 kW (250-320hp), 4TD dengan kapasitas 294 … 331 kW (400 … 450hp) dikembangkan. Varian mesin diesel 5DN dengan kapasitas 331… 367 kW (450-500 hp) untuk kendaraan roda juga dikembangkan. Untuk pengangkut traktor dan kendaraan rekayasa, sebuah proyek dikembangkan untuk mesin diesel 6DN dengan kapasitas 441 … 515 kW (600-700 hp).
Diesel 3TD
Mesin ZTD dalam desain tiga silinder adalah anggota dari satu seri terpadu dengan mesin seri 5TDF, 6TD-1 dan 6TD-2E. Pada awal 60-an, keluarga mesin berdasarkan 5TDF dibuat di Kharkov untuk kendaraan ringan (pengangkut personel lapis baja, kendaraan tempur infanteri, dll.) dan kategori berat (tank, 5TDF, 6TD).
Mesin ini memiliki skema desain tunggal:
- siklus dua langkah;
- susunan horizontal silinder;
- kekompakan tinggi;
- perpindahan panas rendah;
- kemampuan untuk menggunakan pada suhu sekitar
lingkungan dari minus 50 hingga plus 55 °;
- penurunan daya rendah pada suhu tinggi
lingkungan;
- multi-bahan bakar.
Selain alasan objektif, kesalahan dibuat dalam pembuatan keluarga mesin diesel petinju dua langkah 3TD pada pertengahan 60-an. Ide mesin 3 silinder diuji berdasarkan 5 silinder di mana dua silinder teredam. Pada saat yang sama, jalur udara-gas dan unit bertekanan tidak terkoordinasi. Secara alami, kekuatan kerugian mekanis juga meningkat.
Hambatan utama untuk menciptakan keluarga mesin terpadu di tahun 60-an dan 70-an adalah tidak adanya program yang jelas untuk pengembangan pembangunan mesin di negara ini; kepemimpinan "melempar" antara berbagai konsep mesin diesel dan mesin turbin gas.. Pada tahun 70-an, ketika Leonid Brezhnev datang ke kepemimpinan negara, situasinya menjadi lebih buruk, produksi paralel tank dengan mesin yang berbeda - T-72 dan T-80, yang menurut karakteristiknya adalah "tank analog" dari sudah memproduksi T-64. Tidak ada lagi pembicaraan tentang penyatuan mesin tank, kendaraan tempur infanteri, dan pengangkut personel lapis baja.
Sayangnya, situasi yang sama terjadi di cabang lain dari kompleks industri militer - pada saat yang sama, berbagai biro desain sedang dikembangkan dalam peroketan, konstruksi pesawat terbang, sementara yang terbaik tidak dipilih di antara mereka, tetapi produk serupa dari Biro Desain yang berbeda (Biro Desain) diproduksi secara paralel.
Kebijakan seperti itu adalah awal dari akhir ekonomi domestik, dan alasan keterlambatan pembangunan tangki, alih-alih disatukan menjadi "kepalan tunggal", upaya tersebar pada pengembangan paralel biro desain yang bersaing.
Kendaraan ringan (LME), diproduksi pada tahun 60-an … 80-an abad terakhir, memiliki mesin dengan desain yang sudah ketinggalan zaman, memberikan kepadatan daya dalam kisaran 16-20 hp / t. Mesin modern harus memiliki kekuatan spesifik 25-28 hp / t, yang akan meningkatkan kemampuan manuvernya.
Pada 90-an, 2000-an, modernisasi LME menjadi relevan - BTR-70, BTR-50, BMP-2.
Selama periode ini, pengujian mesin-mesin ini dilakukan, yang menunjukkan karakteristik tinggi dari mesin baru, tetapi, pada saat yang sama, sejumlah besar mesin UTD-20S1 disimpan dan diproduksi di wilayah Ukraina setelah keruntuhan. dari Uni Soviet.
Perancang umum untuk pembuatan tangki Ukraina M. D. Borisyuk (KMDB) memutuskan untuk menggunakan mesin serial yang ada - SMD-21 UTD-20 dan "Deutz" Jerman untuk memodernisasi mesin ini.
Setiap kendaraan memiliki mesinnya sendiri yang tidak disatukan satu sama lain dan dengan mesin yang sudah ada di ketentaraan. Alasannya adalah menguntungkan bagi pabrik perbaikan Kementerian Pertahanan untuk menggunakan mesin yang tersedia di gudang pelanggan, sehingga mengurangi biaya pekerjaan.
Tetapi posisi ini kehilangan pekerjaan Perusahaan Negara “Pabrik dinamai V. A. Malysheva”dan, di atas segalanya, pabrik agregat.
Posisi ini ternyata ambigu - di satu sisi, penghematan, di sisi lain, kehilangan perspektif.
Perlu dicatat bahwa dalam KMDB sehubungan dengan 3TD, sejumlah klaim dibuat (untuk kebisingan dan asap), yang diterima dan dihilangkan.
Untuk mengurangi asap selama start-up dan dalam mode transien, peralatan bahan bakar tertutup dipasang pada mesin ZTD dan konsumsi oli berkurang secara signifikan. Pengurangan kebisingan dipastikan dengan mengurangi tekanan pembakaran maksimum dan mengurangi jarak bebas pada pasangan piston-silinder pada mesin 280 dan 400 hp, serta mengurangi kisaran getaran torsi.
Mengurangi konsumsi oli pada mesin ZTD dicapai karena faktor-faktor berikut:
- mengurangi jumlah silinder;
- penggunaan piston dengan bodi besi cor alih-alih paduan aluminium;
- meningkatkan tekanan spesifik cincin pengikis oli dengan
dinding silinder.
Sebagai hasil dari langkah-langkah yang diambil, konsumsi relatif oli pada mesin ZTD mendekati konsumsi pada mesin untuk tujuan ekonomi nasional.