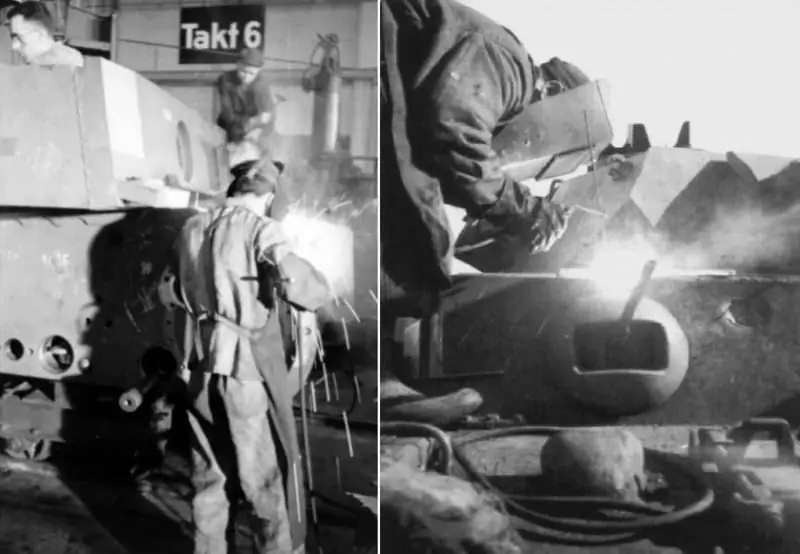
Pendekatan Jerman
Pada bagian pertama materi tentang teknologi pengelasan selama Perang Patriotik Hebat, disebutkan bahwa salah satu pencapaian utama teknologi dan ilmuwan Soviet adalah pengenalan otomatisasi pengelasan lambung tangki dan menara. Di Jerman Nazi, pengelasan otomatis tidak digunakan di pabrik tangki. Ada satu penjelasan yang sangat penting untuk ini - selama periode utama perang, industri tank Reich Ketiga tidak mengalami kekurangan tenaga kerja berkualifikasi tinggi, termasuk tukang las. Dan di Uni Soviet, selama evakuasi perusahaan besar ke timur, personel yang berharga untuk industri hilang, yang membahayakan tidak hanya kualitas perakitan tangki, tetapi bahkan kemungkinan produksi. Di Jerman, sampai pada titik bahwa ketika mengelas lambung tukang las "Panthers" dan "Tigers" ditugaskan untuk jahitan yang terpisah! Insinyur V. V. Ardentov menulis tentang ini dalam materi "Pengalaman Jerman dalam memotong baju besi dan mengelas lambung tangki" di "Buletin industri tangki" pada tahun 1945 yang menang. Karyanya didasarkan pada studi dua pabrik lambung lapis baja di Kirchmeser dan Brandenburg. Jelas, pabrik-pabrik ini mampu membeli kemewahan teknologi seperti itu dalam bentuk tukang las terpisah untuk jahitan terpisah hingga bulan-bulan terakhir perang.
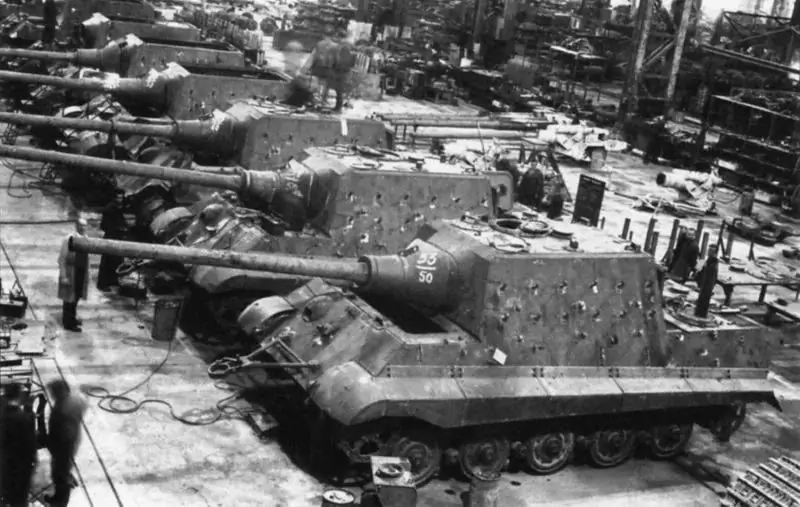
Sebelum mengelas lambung, pelat baja dipotong, yang hingga 1942 dilakukan secara mekanis. Untuk memotong pelat baja untuk koneksi duri-dalam-duri, jauh lebih nyaman menggunakan pemotongan asetilen-oksigen, yang juga digunakan dalam situasi serupa di industri tangki Soviet. Di sini Jerman berada di depan pembuat tank kami baik dalam efisiensi maupun kualitas pemotongan. Ini sebagian besar merupakan hasil dari penggunaan alat berkualitas tinggi (mesin pemotong gas Messer dan Grisheim) dengan kemampuan untuk menyempurnakan ketebalan pelat pelindung. Juga, Jerman menggunakan oksigen dengan pemurnian tingkat tinggi - lebih dari 99%. Akhirnya, dalam proses pemotongan baju besi, Jerman menggunakan beberapa obor, termasuk untuk chamfering. Proses pemotongan api itu sendiri dilakukan secara otomatis - ini memungkinkan untuk mempercepat proses dan membuatnya jauh lebih akurat.
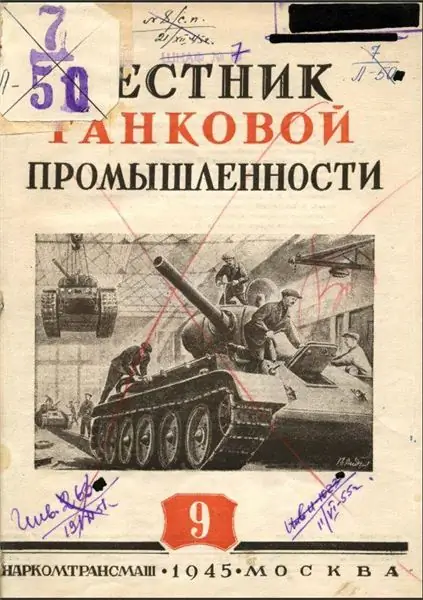
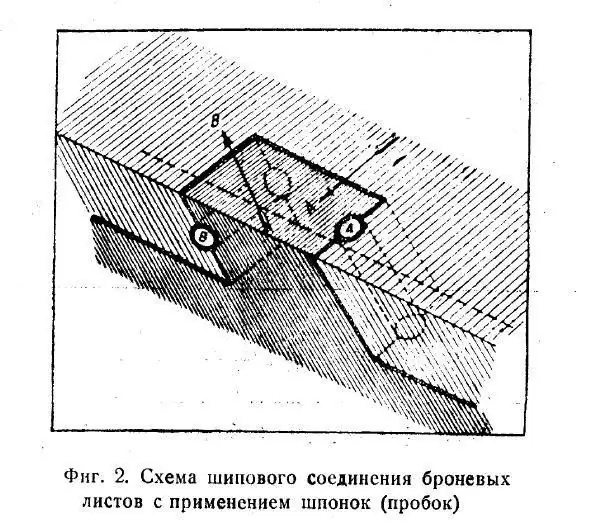
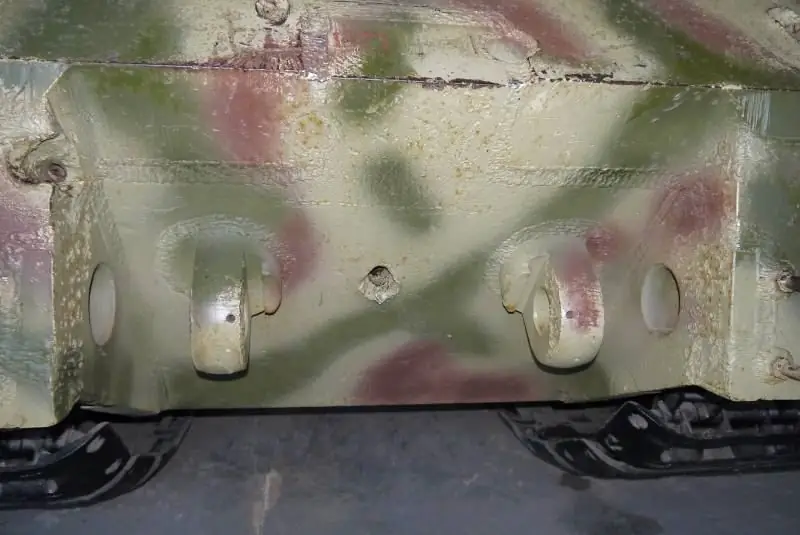
[Tengah]
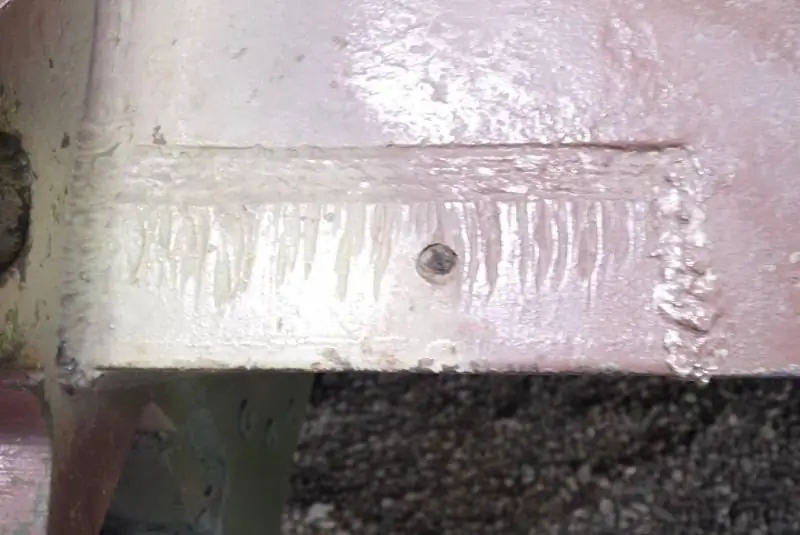
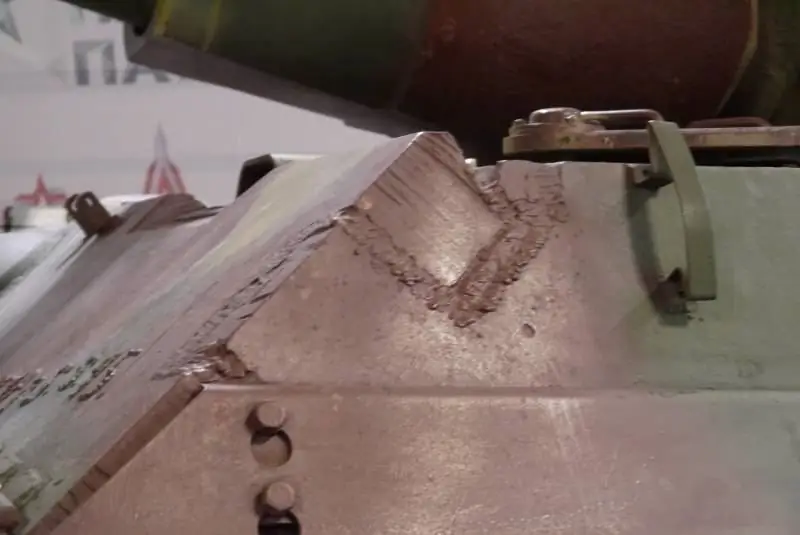
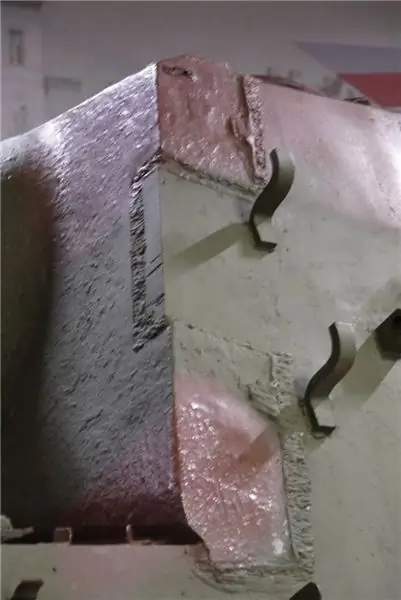
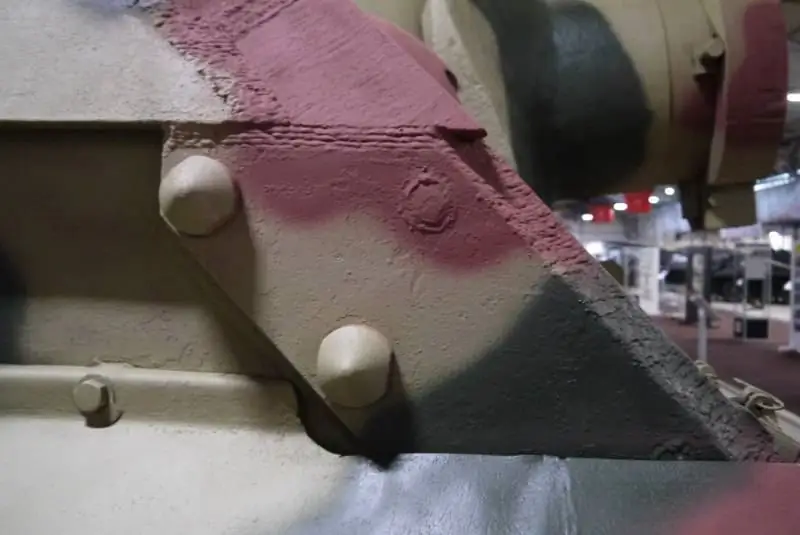
[/Tengah]
Seperti yang Anda ketahui, salah satu fitur pembeda lambung tank Jerman dari tahun 1942 adalah sambungan paku pelat baja dengan paku persegi panjang atau miring. Pada saat yang sama, Jerman tidak terbatas pada artikulasi sederhana - selain itu, untuk kekuatan, kunci atau sumbat silinder dimasukkan ke dalam sambungan. Secara khusus, ini biasa terjadi pada tank menengah "Panther", senjata self-propelled "Ferdinand", menara "Macan" yang berat dan beberapa korps "Maus". Sumbat tersebut adalah gulungan baja dengan diameter hingga 80 mm yang dimasukkan ke dalam sambungan lembaran yang akan disambung setelah dirakit untuk pengelasan. Sumbat ditempatkan di bidang tepi paku pelat pelindung - sepasang diperlukan untuk setiap sambungan. Bahkan, setelah pemasangan kunci, sambungan spike menjadi satu kesatuan bahkan sebelum pengelasan. Dalam hal ini, pasak dipasang rata dengan permukaan dengan pelindung dan dilas di sekeliling alas. Sambungan paku pelat pelindung lambung tangki secara nyata meningkatkan perlindungan balistik dari lapisan las dan pelindung. Pertama-tama, ini dipastikan dengan meningkatkan panjang total lasan, yang terdiri dari segmen terpisah, yang agak mengurangi perambatan retak.
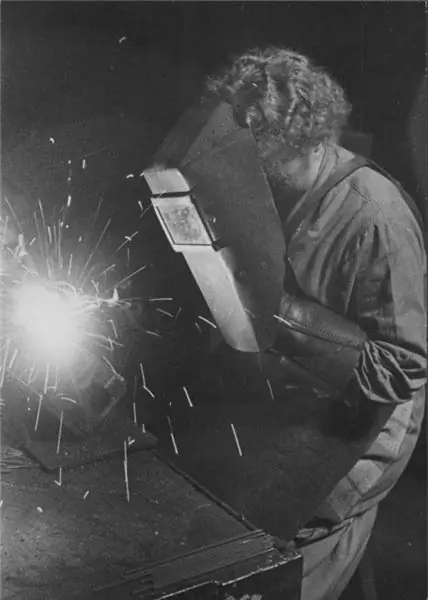
Salah satu masalah dalam pembuatan lambung tank Jerman adalah pembuatan guntingan dan lubang (misalnya, untuk sambungan baju besi yang disebutkan di atas). Tidak mungkin memotongnya dengan gas, jadi pengeboran digunakan. Awalnya, untuk baja kelas E-18 dan E-19, yang menjalani prosedur pengerasan permukaan, umumnya tidak mungkin menemukan bor yang cocok, lapisan luar pelindung ternyata sangat keras. Dalam kasus pengeboran lubang sebelum pendinginan, pendinginan yang tidak merata terbentuk di area lubang, diikuti oleh deformasi dan retak radial. Ya, dan ada retakan pada tank Jerman, dan cukup banyak, dan upaya Jerman untuk menghindarinya akan dibahas nanti. Sebagian, masalah pengerasan baju besi yang tidak merata di area lubang diselesaikan dengan pasta tahan api khusus, yang digunakan untuk menutupi lubang sebelum dikirim ke tungku. Tetapi, sekali lagi, ini hanya menyelesaikan sebagian masalah. Baru pada akhir tahun 1944 di Institut Elektrotermal di Essen masalah ini diselesaikan dengan prosedur temper lokal pada area pelindung yang mengeras. Unit, yang dikembangkan oleh Jerman, dijelaskan dalam artikelnya oleh pemenang Hadiah Stalin, Kandidat Ilmu Teknis A. A. Shmykov. Materi itu diterbitkan dalam edisi khusus “Buletin Industri Tank”, yang dirahasiakan pada masanya dan akrab bagi kita, pada akhir tahun 1945. Pada tahun-tahun pasca-perang, halaman-halaman Vestnik kaya akan analisis terperinci tentang trik-trik teknik para insinyur Jerman, karena ada cukup banyak peralatan yang ditangkap.
Tapi kembali ke rilis lokal dari baju besi di mana lubang dibor. Dasar dari unit ini adalah elektroda grafit yang terhubung ke lokasi pengeboran, di mana arus listrik 220 ampere dan tegangan 380 volt dilewatkan. Akibatnya, baju besi dipanaskan sampai suhu temper. Bergantung pada ketebalan baju besi dan diameter lubang, ini membutuhkan waktu 7 hingga 15 menit. Setelah prosedur temper, kekerasan armor menurun 2-2,5 kali. Patut dicatat bahwa industri dalam negeri (termasuk industri tangki) juga menggunakan tempering baja dengan memanaskan arus - "pengetahuan" Jerman hanya dalam penggunaan elektroda grafit.
Jerman dan elektroda
Jerman juga menggunakan liburan saat mengelas lembaran baja kekerasan tinggi mereka dengan kandungan karbon di kisaran 0,40-0,48%. Ini diketahui oleh spesialis TsNII-48 (Lembaga Lapis Baja) selama perang, ketika insinyur metalurgi mencari resep untuk mengurangi keretakan pada baju besi T-34. Ternyata, Jerman melepaskan pelat baja pada suhu 500-600 derajat (liburan tinggi), dan kemudian mengelas baju besi yang dipanaskan hingga 150-200 derajat dalam beberapa lintasan. Tukang las tidak menggunakan elektroda dengan diameter lebih dari 5 mm - sulit dipercaya, mengingat ketebalan baju besi tank Jerman. Elektroda dengan diameter 4 mm bekerja pada arus 120-140 ampere, dengan diameter 5-6 mm - 140-160 ampere. Teknologi ini memungkinkan untuk tidak terlalu panas di area las. Ini berarti diperoleh zona pengerasan dan temper yang lebih kecil. Selain itu, setelah pengelasan, jahitan mendingin dengan sangat lambat - semua ini akhirnya memungkinkan Jerman untuk lebih atau kurang berhasil menangani retakan di tempat sambungan las. Selain itu, elektroda austenitik sebagian besar digunakan, yang menyebabkan daktilitas las yang tinggi dan transisi yang berkepanjangan ke keadaan martensit rapuh. Insinyur TsNII-48 dengan sangat hati-hati mempelajari fitur-fitur siklus teknologi pengelasan pelindung tangki, yang memungkinkan untuk berhasil mentransfer teknik-teknik ini ke siklus produksi T-34. Secara alami, tidak ada seorang pun di industri tangki yang mampu menerapkan lapisan las berlapis-lapis yang begitu melelahkan di seluruh lambung tangki, "know-how" Jerman hanya digunakan pada lapisan paling kritis yang rentan terhadap retak.
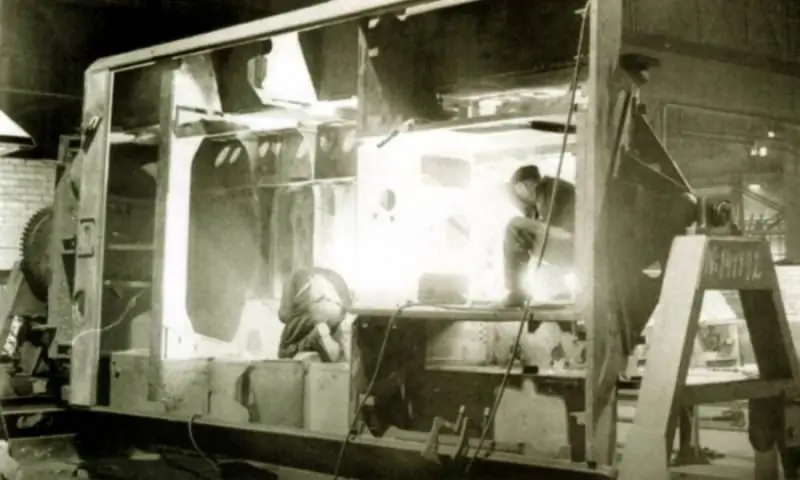
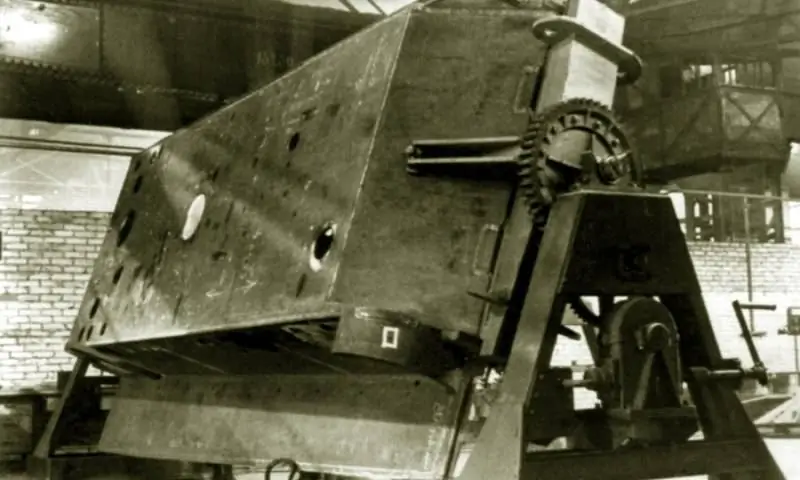
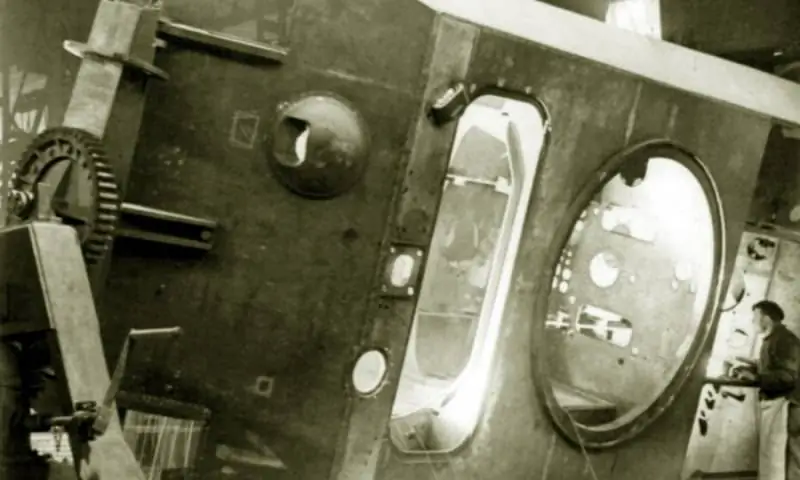
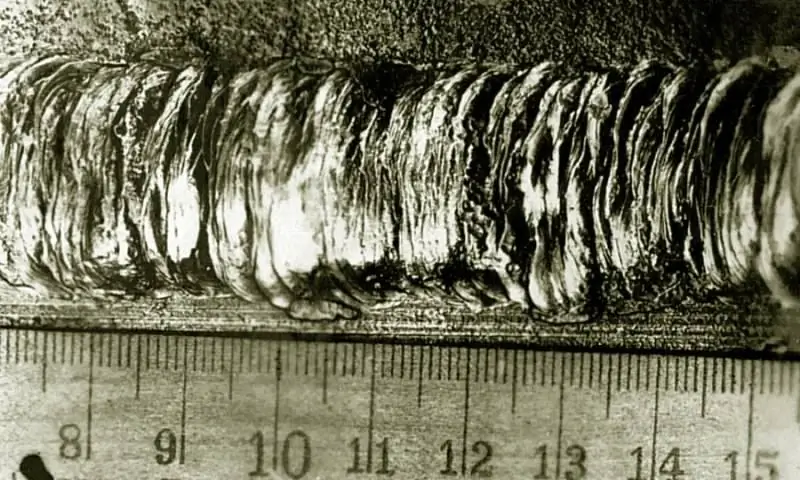
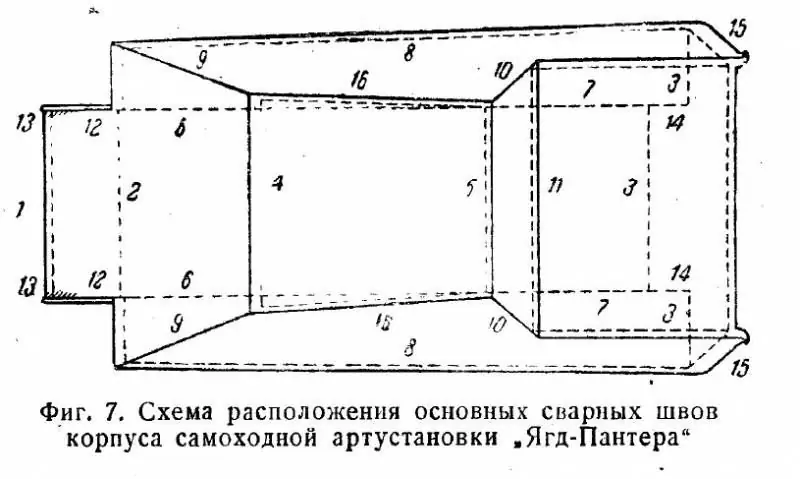
Jerman melakukan pengelasan lambung tangki dalam kondisi yang cukup nyaman pada kemiringan besar tanpa paku payung awal (walaupun dalam beberapa kasus mereka masih melewati elektroda 5 mm di sepanjang sambungan). Miring adalah struktur di mana, seperti di atas ludah, bangkai tank Jerman berputar di sekitar sumbu memanjang. Drive itu manual atau listrik. Karena akurasi pemotongan yang tinggi, celah antara bagian-bagian tubuh yang dipasang pada rotator tidak melebihi (setidaknya pada periode utama perang) 3-4 mm. Jika tidak, gasket proses baja digunakan. Jahitan panjang dipecah oleh tukang las menjadi beberapa yang kecil dan dilas secara bersamaan dalam satu arah. Lapisan penutup juga dilas oleh dua tukang las secara serempak satu sama lain. Ini memastikan tegangan pengerasan minimum dari baja dan distribusi yang paling seragam. Menurut salah satu legenda, disuarakan oleh Alexander Volgin dalam materi "Frame for the German Menagerie", gaji tukang las di beberapa perusahaan Reich Ketiga adalah pekerjaan sepotong-sepotong - untuk massa logam yang disimpan di tangki.
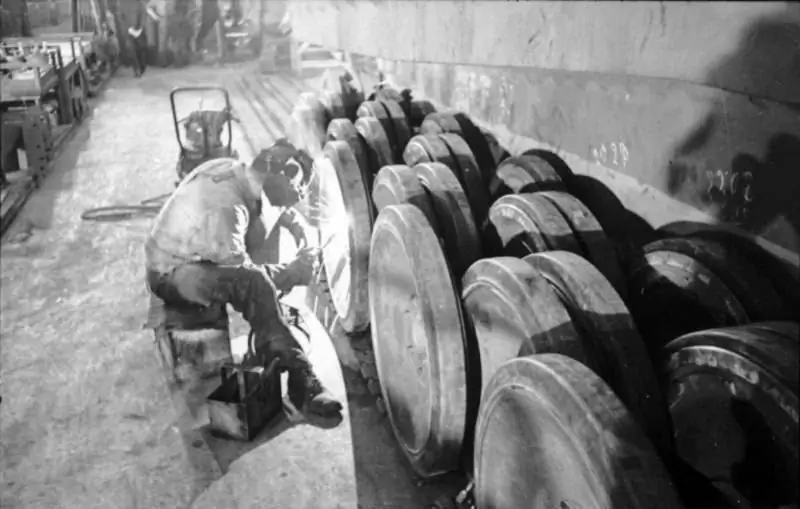
Tidak perlu membicarakan aturan khusus untuk mengontrol lapisan las di industri tangki Jerman - tidak ada sinar-X, tidak ada deteksi cacat magnet, tidak ada pengeboran primitif. Dan ada retakan di jahitannya! Jika panjangnya mencapai 100 mm, maka mereka digiling dan dilas, dan jika lebih, maka mereka dilebur dengan busur listrik dan juga dilas. Mereka juga melakukan hal yang sama dengan retakan yang terdeteksi secara visual di armor utama. Ngomong-ngomong, seiring waktu, Jerman berhasil mengurangi proporsi retakan pada lapisan yang dilas dari 30-40% menjadi 10-20% karena komposisi elektroda baru. Juga digunakan adalah pergantian lintasan dalam lasan multilayer dengan elektroda austenitik dan ferit.