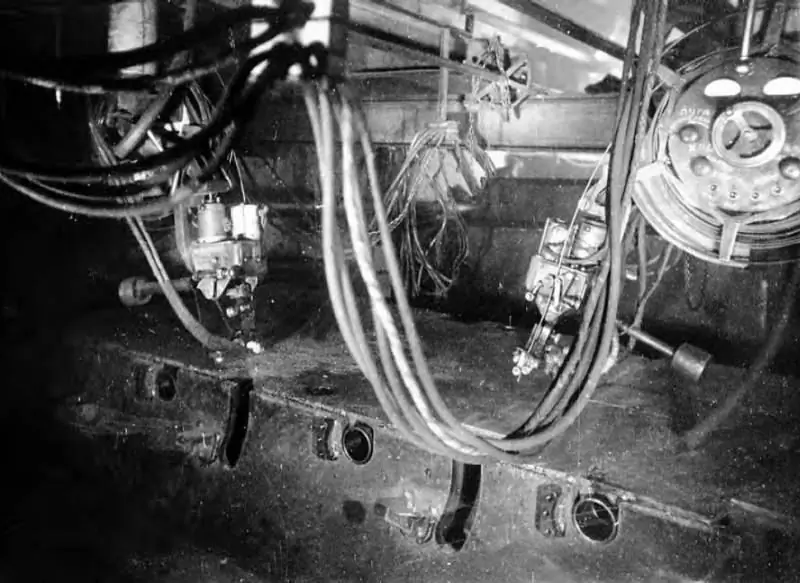
Menjinakkan Armor
Salah satu masalah utama dalam produksi lambung dan menara tangki menengah T-34 adalah retak pada bagian yang dilas. Ini semua tentang kekerasan tinggi pelindung 8C, ketika robekan kecil atau retakan mikro terbentuk di sebelah jahitan yang dilas. Kehadiran tegangan sisa setelah pengelasan pertama kali setelah produksi kendaraan lapis baja tidak membuat dirinya terasa, tetapi seiring waktu ia keluar dengan retakan hingga panjang 500 mm. Semua ini, tentu saja, mengurangi ketahanan benturan pelindung tank. Untuk mengatasi masalah ini, segera setelah organisasi produksi perusahaan yang dievakuasi, pada paruh kedua tahun 1942, para spesialis dari Institut Lapis Baja (TsNII-48) dan Institut Pengelasan Listrik dari Akademi Ilmu Pengetahuan Uni Soviet tertarik. Penelitian dilakukan di dua perusahaan: Pabrik Tangki Ural No. 183 di Nizhny Tagil dan Pabrik Teknik Berat Ural di Sverdlovsk. Secara total, dari Juli hingga Oktober, ahli metalurgi dan ilmuwan material menyelidiki pembentukan retakan selama pengelasan sekitar 9.500 bagian lapis baja. Tujuan dari penelitian ini adalah untuk menemukan komposisi kimia paling optimal dari armor 8C. Ternyata komponen terpenting dalam baju besi dalam situasi ini adalah karbon. Jika isinya di baju besi lebih dari 0,25%, kekerasan zona yang mengeras di area jahitan yang dilas meningkat tajam, yang pasti menyebabkan retak.
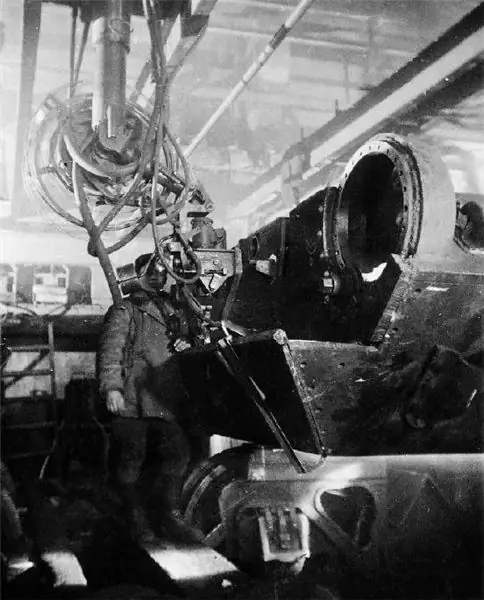
Tetapi tidak mudah untuk memastikan kandungan karbon rendah seperti itu dalam baja lapis baja di masa damai, dan di masa perang tampaknya mustahil sama sekali. Perubahan kecil "kosmetik" dalam siklus pengelasan melalui penggunaan elektroda austenitik, sistem multi-gulungan untuk menerapkan lapisan las, dan temper yang rendah pada rakitan setelah pengelasan memungkinkan untuk menaikkan batas atas kandungan karbon hanya menjadi 0,28%. Ngomong-ngomong, di industri tank Jerman mereka bahkan tidak mendengar tentang persyaratan serius untuk pelindung tank - rata-rata, bagian karbon berada di kisaran 0,4-0,5%. Solusi untuk masalah munculnya retakan di area pengelasan adalah pemanasan awal bagian hingga 150-200 derajat Celcius, diikuti dengan pendinginan perlahan bagian setelah pengelasan hingga 100 derajat selama 30 menit. Untuk tujuan ini, Institut Lapis Baja mengembangkan induktor khusus yang menyediakan pemanasan lokal bagian lapis baja di zona pemotongan atau pengelasan gas. Di Pabrik Pembuatan Mesin Berat Ural, induktor digunakan untuk mengelas sambungan bagian depan dengan sisi dan atap, serta saat memotong lubang penyeimbang di bagian samping tangki yang mengeras. Dengan demikian, masalah retak selama pengelasan baja lapis baja karbon sedang diselesaikan. Seiring waktu, praktik pabrik Sverdlovsk diperluas ke pabrik tangki lainnya.
Mesin las
Pada Juli 1941, atas perintah Dewan Komisaris Rakyat, Institut Pengelasan Listrik dari Akademi Ilmu Pengetahuan Uni Soviet dievakuasi ke Nizhny Tagil. Itulah sebabnya pengelasan busur otomatis lambung tangki diperkenalkan di Uralvagonzavod untuk pertama kalinya. Tentu saja, teknologi ini sudah diketahui sebelumnya, tetapi kelompok Akademisi Yevgeny Oskarovich Paton dengan karyawan TsNII-48 dapat mengadaptasinya untuk mengelas baja lapis baja. Salah satu ilmuwan terkemuka yang berkontribusi pada pengembangan pengelasan lapis baja adalah Vladimir Ivanovich Dyatlov. Bersama dengan karyawan Pabrik Komintern Kharkov, ia memecahkan masalah keretakan pada baju besi selama pengelasan dengan memasukkan kawat karbon rendah ke dalam kolam las (lebih lanjut tentang ini di bawah). Pada tahun 1942, seorang ilmuwan, yang pertama di dunia, menemukan fenomena pengaturan diri proses busur dengan elektroda yang dapat dikonsumsi, yang memungkinkan untuk secara signifikan menyederhanakan desain mekanisme pengumpanan mesin las. Juga, karena ini, dimungkinkan untuk membuat kepala las motor tunggal yang relatif sederhana, lebih andal dan lebih murah. Tanpa Dyatlov, tidak mungkin membuat fluks efektif berdasarkan terak tungku arang tanur sembur dari pabrik metalurgi Ashinskiy, yang diberi nama "fluks terak ". Sejak Oktober 1943, ilmuwan mengepalai laboratorium pengelasan Uralvagonzavod dan tetap di posisi ini hingga 1944, sampai ia dipindahkan ke Institut Penelitian Pusat Teknologi Pembuatan Kapal.
Tetapi kembali ke T-34 yang legendaris, yang tidak akan pernah menjadi tangki sebesar itu, jika bukan karena pengelasan otomatis lambung lapis baja (menara) di pabrik No. 183 dan UZTM. Penggunaan mesin las otomatis memungkinkan untuk mengurangi waktu pengelasan sebesar 3-6,5 kali. Pada saat yang sama, setidaknya 40 meter linier lapisan las digunakan untuk setiap korps tangki.
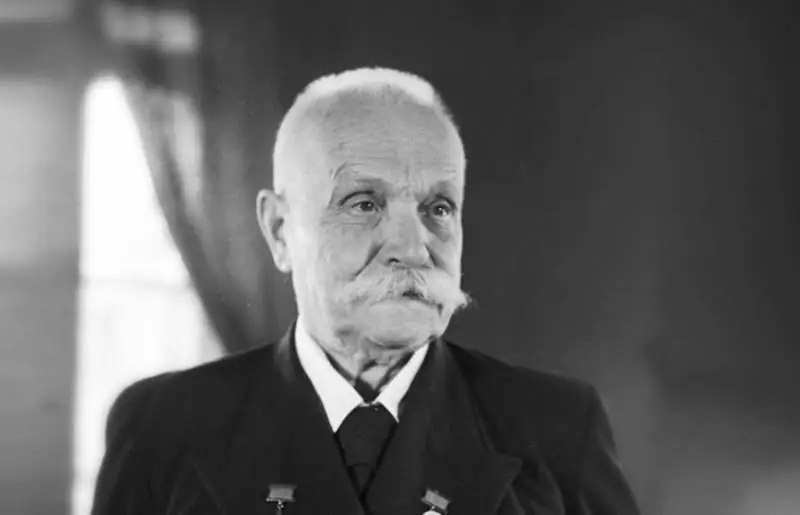
Selain T-34, pengelasan Academician Paton digunakan di pabrik lambung lapis baja No. 200 di Chelyabinsk. Dengan bantuannya, bagian bawah lambung tangki KV dimasak, yang totalnya mencapai sekitar 15 meter jahitan per kendaraan. Adalah penting bahwa otomatisasi pengelasan baju besi memungkinkan untuk menarik pekerja berketerampilan rendah ke produksi - tukang las utama selama perang ada kekurangan kronis. Sejak Juli 1942, konveyor tangki unik telah beroperasi di Nizhny Tagil, di mana 19 unit las busur terendam otomatis dioperasikan. Perkirakan skala inovasi - ini membebaskan 280 tukang las berkualitas tinggi untuk pekerjaan lain, menggantikan mereka dengan 57 pekerja berketerampilan rendah. Akademisi Yevgeny Oskarovich Paton sendiri dalam sebuah memo yang ditujukan kepada sekretaris departemen industri tangki dari komite regional Sverdlovsk dari Partai Komunis Semua-Serikat Bolshevik pada Maret 1942 berbicara tentang keefektifan pengenalan pengelasan otomatis (kutipan dari N. Melnikov's buku "Industri tank Uni Soviet selama Perang Patriotik Hebat"):
"Karena produktivitas tinggi pengelasan otomatis berkecepatan tinggi di bawah lapisan fluks, waktu untuk mengelas tubuh akan berkurang secara signifikan, dan konsumsi tenaga kerja, listrik, dan kawat elektroda akan berkurang."
Perbandingan waktu yang dihabiskan untuk pengelasan manual dan otomatis dapat ditemukan di arsip kompleks pameran OAO NPK Uralvagonzavod. Menurut mereka, dibutuhkan tukang las lebih dari lima jam untuk mengelas, misalnya, sektor tali bahu turret T-34, dan pengelasan otomatis dapat melakukan ini hanya dalam 40 menit. Sambungan bawah dilas secara manual dalam tiga jam, dan dalam mode otomatis - dalam satu jam.
Berjuang untuk jahitannya
Tidak dapat dikatakan bahwa mesin las otomatis tiba-tiba muncul di pabrik perakitan industri tangki Soviet. Pertama, pangsa pengelasan manual masih sangat besar dalam produksi produk lapis baja, dan kedua, pada awalnya, tidak semuanya mulus dengan teknologi itu sendiri. Itu tidak mungkin untuk memberikan lasan tingkat keuletan yang diperlukan - setelah pendinginan, menjadi keras dan rapuh. Ini, tentu saja, memiliki efek paling negatif pada ketahanan proyektil armor. Setelah menganalisis alasannya, ternyata itu semua tentang melebihi kedalaman penetrasi logam yang dilas, mencampur logam kawat dengan logam dasar dan paduan yang signifikan dari logam las. Kelompok-kelompok dari TsNII-48 di bawah kepemimpinan I. F. Sribny dan dari Institute of Welding, yang dipimpin oleh V. I. Dyatlov yang disebutkan di atas, mengusulkan dan menguji metode pengelasan "bandel" armor 8C dan 2P berikut. Pertama-tama, ini adalah pengelasan multi-pass, ketika mesin menghubungkan bagian-bagian yang akan dilas dalam beberapa langkah. Ini memastikan penetrasi sambungan yang rendah dan pembentukan jahitan yang kuat dan fleksibel. Jelas bahwa teknik seperti itu bukan yang paling efektif dalam kondisi masa perang: bagaimanapun, pengelasan multi-pass membutuhkan banyak waktu dibandingkan dengan single-pass.
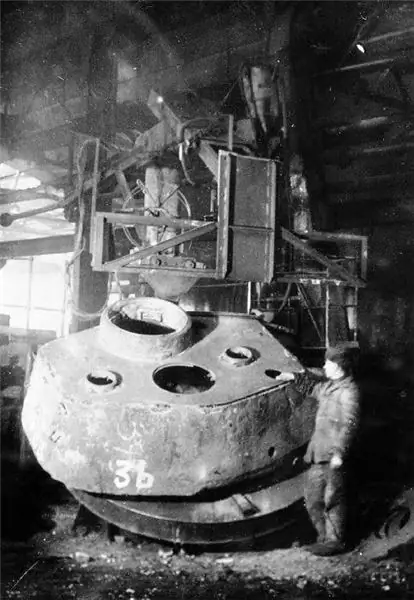
Teknik kedua dari TsNII-48 dan Institute of Welding adalah peletakan kawat baja karbon rendah di alur jahitan untuk mengurangi "kepudaran" logam pelindung. Akibatnya, jahitan setelah pendinginan menjadi lebih plastis, kawat secara serius mengurangi suhu di dalam alur jahitan, dan juga menggandakan produktivitas mesin las. Ini ternyata menjadi teknik yang paling efektif, yang bahkan lebih ditingkatkan. Metode pengelasan baru "dalam dua kabel", di mana kabel kedua (pengisi), tidak terhubung ke sumber arus, dimasukkan ke dalam kolam las pada sudut ke kawat elektroda. Umpan dan diameter kawat kedua dihitung sehingga jumlah logam yang diendapkan darinya sama dengan jumlah logam dari kawat elektroda yang diendapkan, yaitu diameter kawat kedua harus sama dengan diameter elektroda kawat dan tingkat umpan mereka harus sama. Namun, karena kebutuhan untuk melengkapi kembali kepala otomatis dari mengumpankan satu kawat ke memberi makan dua kabel, pengenalan metode ini ditunda dan diganti dengan metode dengan penyisipan batang. Namun demikian, sudah pada bulan Juni-Juli 1942, metode ini diterapkan di pabrik No. 183 saat mengelas sejumlah pelat bawah hidung lambung tangki dengan balok busur.
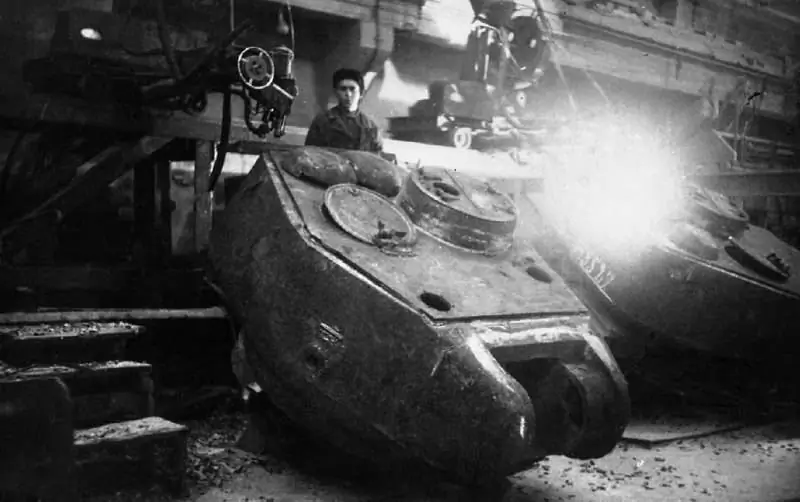
Kesulitan dengan otomatisasi pengelasan korps tank (menara) juga organisasi. Perlu diingat bahwa mesin las belum pernah dirakit secara seri sebelumnya dan, pada kenyataannya, merupakan produk dari produksi percontohan Institute of Welding. Ini menjelaskan beberapa kelambatan dalam pengembangan teknologi baru di industri tangki. Jadi, pada akhir 1942, pabrik tangki hanya memiliki 30 hingga 35 mesin las, yang tentu saja tidak cukup. Oleh karena itu, Komisaris Rakyat IM Zaltsman, atas perintah No. 200 tanggal 28 Maret 1943, memerintahkan di pabrik No. 183 untuk memasang tambahan 7 unit las otomatis pada pertengahan Mei, di Pabrik Pembangunan Mesin Berat Ural pada tanggal 1 Juni. mesin otomatis dan pada 15 Juni, 5 unit diminta untuk dikirim ke pabrik Chelyabinsk No. 200. Langkah ini adalah salah satu dari banyak yang memungkinkan industri tank domestik untuk mencapai target produksi yang direncanakan untuk kendaraan lapis baja tracked yang sangat dibutuhkan untuk bagian depan.