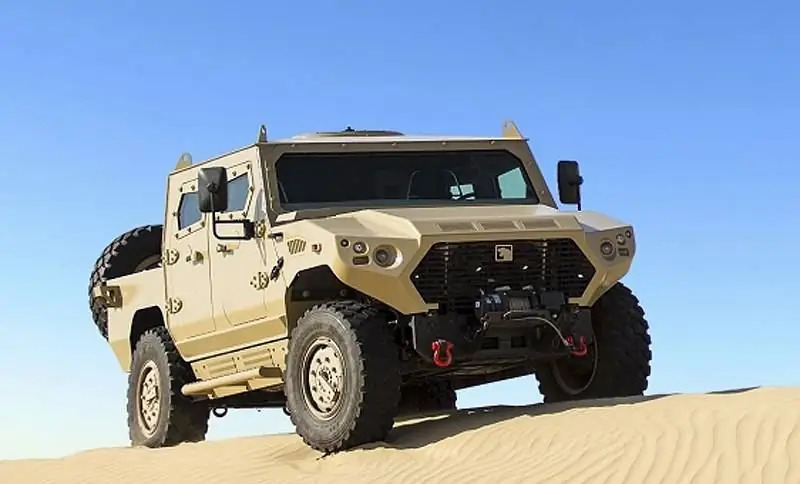
Armor jutaan tahun lebih tua dari manusia, dan itu dikembangkan terutama untuk melindungi dari rahang dan cakar. Ada kemungkinan bahwa buaya dan kura-kura sebagian dapat menginspirasi manusia untuk menciptakan elemen pelindung. Semua senjata energi kinetik, baik itu tongkat prasejarah atau proyektil penusuk baju besi, dirancang untuk memusatkan kekuatan besar di area kecil, tugasnya adalah menembus target dan menimbulkan kerusakan maksimum padanya. Akibatnya, tugas pelindung adalah untuk mencegah hal ini dengan membelokkan atau menghancurkan sarana penyerang dan/atau menyebarkan energi tumbukan ke area seluas mungkin untuk meminimalkan kerusakan pada tenaga kerja, sistem transportasi, dan struktur yang dilindunginya.
Armor modern biasanya terdiri dari lapisan luar yang keras untuk menghentikan, membelokkan, atau menghancurkan proyektil, lapisan perantara dengan "pekerjaan untuk memecahkan" yang sangat tinggi, dan lapisan dalam yang kental untuk mencegah retakan dan serpihan.
Baja
Baja, yang menjadi bahan pertama yang banyak digunakan dalam pembuatan kendaraan lapis baja, masih diminati, meskipun munculnya baju besi berdasarkan paduan ringan aluminium dan titanium, keramik, komposit dengan matriks polimer, diperkuat dengan serat kaca, aramid dan polietilen dengan berat molekul sangat tinggi, serta bahan komposit dengan matriks logam.
Banyak pabrik baja, termasuk SSAB, terus mengembangkan baja berkekuatan tinggi untuk berbagai aplikasi kritis berat seperti selubung tambahan. Kelas baja lapis baja ARM OX 600T, tersedia dalam ketebalan 4-20 mm, tersedia dengan kekerasan yang dijamin 570 hingga 640 unit HBW (singkatan untuk Hardness, Brinell, Wolfram; tes di mana bola tungsten dengan diameter standar ditekan menjadi sampel bahan dengan kekuatan yang diketahui, kemudian diameter ceruk yang terbentuk diukur; kemudian parameter ini diganti ke dalam rumus, yang memungkinkan Anda untuk mendapatkan jumlah unit kekerasan).
SSAB juga menekankan pentingnya mencapai keseimbangan yang tepat antara kekerasan dan ketangguhan untuk penetrasi dan perlindungan terhadap ledakan. Seperti semua baja, ARMOX 600T terdiri dari besi, karbon dan sejumlah komponen paduan lainnya termasuk silikon, mangan, fosfor, belerang, kromium, nikel, molibdenum, dan boron.
Ada batasan pada teknik manufaktur yang digunakan, terutama dalam hal suhu. Baja ini tidak dimaksudkan untuk perlakuan panas tambahan; jika dipanaskan di atas 170 ° C setelah pengiriman, SSAB tidak dapat menjamin sifat-sifatnya. Perusahaan yang dapat mengatasi pembatasan semacam ini kemungkinan akan menarik pengawasan ketat dari produsen kendaraan lapis baja.
Perusahaan Swedia lainnya, Deform, menawarkan suku cadang hot-formed baja tahan peluru kepada produsen kendaraan lapis baja, terutama mereka yang ingin meningkatkan perlindungan kendaraan komersial / sipil.
Firewall Deform one-piece dipasang di Nissan PATROL 4x4, minibus Volkswagen T6 TRANSPORTER, dan truk pikap Isuzu D-MAX, bersama dengan lembaran lantai yang kokoh dari bahan yang sama. Proses pembentukan panas yang dikembangkan oleh Deform dan digunakan dalam produksi lembaran mempertahankan kekerasan 600HB [HBW].
Perusahaan mengklaim bahwa itu dapat memulihkan sifat semua baja pelindung di pasar sambil mempertahankan bentuk yang ditentukan secara struktural, sementara bagian yang dihasilkan jauh lebih unggul daripada struktur las tradisional dan sebagian tumpang tindih. Dalam metode yang dikembangkan oleh Deform, lembaran dipadamkan dan ditempa setelah penempaan panas. Berkat proses ini, dimungkinkan untuk mendapatkan bentuk tiga dimensi yang tidak dapat diperoleh dengan pembentukan dingin tanpa keharusan dalam kasus seperti "lasan yang melanggar integritas titik kritis".
Deformasi lembaran baja panas telah digunakan pada BAE Systems BVS-10 dan CV90 dan, sejak awal 1990-an, pada banyak mesin Kraus-Maffei Wegmann (KMW). Pesanan datang untuk produksi pelat baja tiga dimensi untuk tangki LEOPARD 2 dan beberapa pelat berbentuk untuk kendaraan BOXER dan PUMA, ditambah untuk beberapa kendaraan Rheinmetall, termasuk lagi BOXER, serta palka untuk kendaraan WIESEL. Deform juga bekerja dengan bahan pelindung lainnya termasuk aluminium, kevlar / aramid dan titanium.
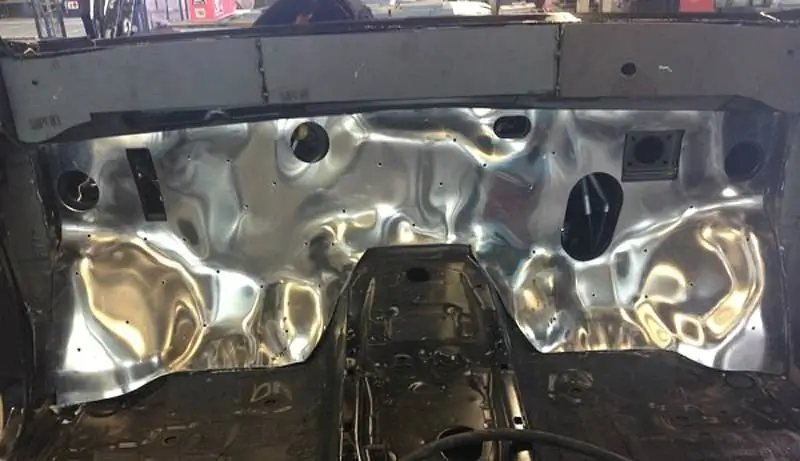
Kemajuan aluminium
Sedangkan untuk kendaraan lapis baja, untuk pertama kalinya lapis baja aluminium banyak digunakan dalam pembuatan pengangkut personel lapis baja M113, yang telah diproduksi sejak 1960. Itu adalah paduan, ditunjuk 5083, mengandung 4,5% magnesium dan jumlah yang jauh lebih kecil dari mangan, besi, tembaga, karbon, seng, kromium, titanium dan lain-lain. Meskipun 5083 mempertahankan kekuatannya dengan baik setelah pengelasan, itu bukan paduan yang dapat diolah dengan panas. Ia tidak memiliki ketahanan yang baik terhadap peluru penusuk lapis baja 7,62mm, tetapi, seperti yang dikonfirmasi oleh tes resmi, ia menghentikan peluru penusuk lapis baja gaya Soviet 14,5mm lebih baik daripada baja, sekaligus menghemat berat dan menambah kekuatan yang diinginkan. Untuk tingkat perlindungan ini, lembaran aluminium lebih tebal dan 9 kali lebih kuat dari baja dengan kepadatan lebih rendah 265 r / cm3, yang menghasilkan pengurangan berat struktur.
Produsen kendaraan lapis baja segera mulai meminta lapis baja aluminium yang lebih ringan, lebih kuat secara balistik, dapat dilas, dan tahan panas, yang menyebabkan pengembangan Alcan 7039 dan kemudian 7017, keduanya dengan kandungan seng yang lebih tinggi.
Seperti baja, stamping dan perakitan selanjutnya dapat berdampak negatif pada sifat pelindung aluminium. Saat pengelasan, zona yang terkena panas melunak, tetapi kekuatannya dipulihkan sebagian karena pengerasan selama penuaan alami. Struktur logam berubah di zona sempit di dekat lasan, menciptakan tegangan sisa yang besar jika terjadi kesalahan pengelasan dan / atau perakitan. Akibatnya, teknik manufaktur harus meminimalkannya, sementara risiko retak korosi tegangan juga harus diminimalkan, terutama ketika umur desain mesin diharapkan lebih dari tiga dekade.
Perengkahan korosi tegangan adalah proses munculnya dan pertumbuhan retakan di lingkungan korosif, yang cenderung memburuk dengan bertambahnya jumlah elemen paduan. Pembentukan retakan dan pertumbuhan selanjutnya terjadi sebagai akibat dari difusi hidrogen di sepanjang batas butir.
Penentuan kerentanan terhadap retak dimulai dengan ekstraksi sejumlah kecil elektrolit dari retakan dan analisisnya. Tes korosi tegangan tingkat regangan rendah dilakukan untuk menentukan seberapa parah paduan tertentu telah rusak. Peregangan mekanis dari dua sampel (satu di lingkungan korosif, dan yang lainnya di udara kering) terjadi sampai gagal, dan kemudian deformasi plastis di lokasi fraktur dibandingkan - semakin banyak sampel diregangkan hingga gagal, semakin baik.
Ketahanan terhadap retak korosi tegangan dapat ditingkatkan selama pemrosesan. Misalnya, menurut Total Materia, yang menyebut dirinya "database material terbesar di dunia," Alcan telah meningkatkan kinerja 7017 dalam uji retak korosi tegangan yang dipercepat sebanyak 40 kali. Hasil yang diperoleh juga memungkinkan untuk mengembangkan metode perlindungan korosi untuk zona struktur yang dilas, di mana sulit untuk menghindari tegangan sisa. Penelitian yang bertujuan untuk meningkatkan paduan untuk mengoptimalkan karakteristik elektrokimia sambungan las sedang berlangsung. Bekerja pada paduan baru yang dapat diberi perlakuan panas berfokus pada peningkatan kekuatan dan ketahanan korosi, sementara bekerja pada paduan yang tidak dapat diolah panas bertujuan untuk menghilangkan kendala yang dikenakan oleh persyaratan kemampuan las. Bahan terberat dalam pengembangan akan menjadi 50% lebih kuat dari pelindung aluminium terbaik yang digunakan saat ini.
Paduan kepadatan rendah seperti aluminium lithium menawarkan penghematan berat sekitar 10% dibandingkan paduan sebelumnya dengan ketahanan peluru yang sebanding, meskipun kinerja balistik belum sepenuhnya dievaluasi menurut Total Materia.
Metode pengelasan, termasuk yang robotik, juga meningkat. Di antara tugas-tugas yang diselesaikan adalah meminimalkan pasokan panas, busur las yang lebih stabil karena peningkatan sistem pasokan energi dan kawat, serta pemantauan dan pengendalian proses oleh sistem pakar.
MTL Advanced Materials bekerja dengan ALCOA Defense, produsen pelat baja aluminium terkenal, untuk mengembangkan apa yang digambarkan perusahaan sebagai "proses pembentukan dingin yang andal dan dapat diulang." Perusahaan mencatat bahwa paduan aluminium yang dikembangkan untuk aplikasi pelindung tidak dirancang untuk pembentukan dingin, yang berarti proses barunya akan membantu menghindari mode kegagalan umum, termasuk retak. Tujuan utamanya adalah untuk memungkinkan perancang mesin meminimalkan kebutuhan akan pengelasan dan mengurangi jumlah suku cadang, menurut perusahaan. Mengurangi volume pengelasan, perusahaan menekankan, meningkatkan kekuatan struktural dan perlindungan kru sekaligus mengurangi biaya produksi. Dimulai dengan paduan 5083-H131 yang telah terbukti dengan baik, perusahaan mengembangkan proses untuk bagian pembentuk dingin dengan sudut lengkung 90 derajat di sepanjang dan melintasi butiran, kemudian beralih ke bahan yang lebih kompleks, misalnya, paduan 7017, 7020, dan 7085, juga mencapai hasil yang baik.
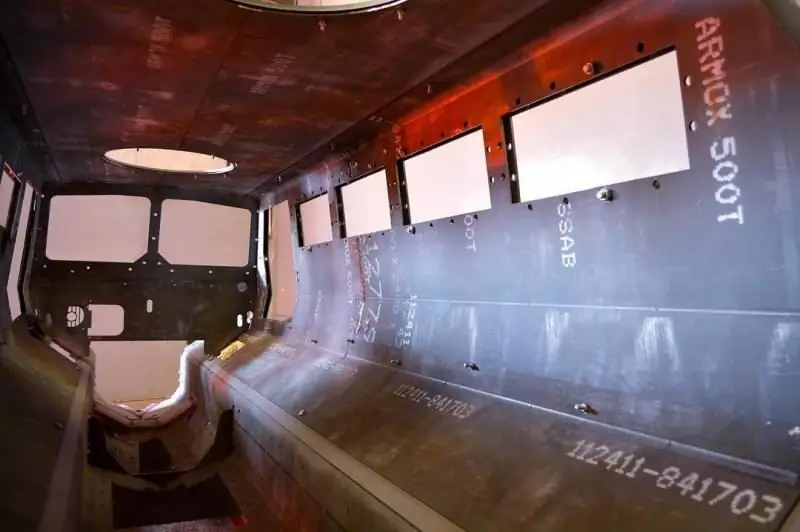
Keramik dan komposit
Beberapa tahun yang lalu, Morgan Advanced Materials mengumumkan pengembangan beberapa sistem pelindung SAMAS, yang terdiri dari kombinasi keramik canggih dan komposit struktural. Lini produk meliputi pelindung berengsel, pelapis anti-fragmentasi, kapsul kemampuan bertahan yang terbuat dari komposit struktural untuk mengganti lambung logam dan melindungi modul senjata, baik yang berpenghuni maupun tidak berpenghuni. Semuanya dapat disesuaikan dengan kebutuhan khusus atau dibuat sesuai pesanan.
Memberikan perlindungan STANAG 4569 Level 2-6, bersama dengan kinerja multi-dampak dan penghematan berat (perusahaan mengklaim sistem ini memiliki berat setengah dari produk baja serupa), dan beradaptasi dengan ancaman, platform, dan misi tertentu. … Pelapis anti pecah dapat dibuat dari panel datar dengan berat 12,3 kg untuk menutupi area 0,36 m2 (sekitar 34 kg / m2) atau fitting padat dengan berat 12,8 kg untuk 0,55 m2 (sekitar 23,2 kg / m2).
Menurut Morgan Advanced Materials, armor tambahan yang dirancang untuk baru dan modernisasi platform yang ada menawarkan kemampuan yang sama dengan setengah bobot. Sistem yang dipatenkan memberikan perlindungan maksimal terhadap berbagai ancaman, termasuk senjata kaliber kecil dan menengah, perangkat peledak improvisasi (IED) dan granat berpeluncur roket, serta kinerja multi-dampak.
Sistem pelindung "semi-struktural" dengan ketahanan korosi yang baik ditawarkan untuk modul senjata (selain aplikasi udara dan laut), dan bersama dengan penghematan berat dan meminimalkan masalah dengan pusat gravitasi, tidak seperti baja, sistem ini menciptakan lebih sedikit masalah kompatibilitas elektromagnetik.
Perlindungan modul senjata adalah masalah khusus, karena mereka adalah target yang menarik, karena penonaktifan mereka secara drastis merusak komando kru terhadap situasi dan kemampuan kendaraan untuk menghadapi ancaman di sekitar. Mereka juga memiliki optoelektronik yang halus dan motor listrik yang rentan. Karena biasanya dipasang di bagian atas kendaraan, pelindung harus ringan untuk menjaga pusat gravitasi serendah mungkin.
Sistem perlindungan modul senjata, yang dapat mencakup kaca lapis baja dan perlindungan bagian atas, dapat dilipat sepenuhnya, dua orang dapat memasangnya kembali dalam 90 detik. Kapsul survivabilitas komposit dibuat dari apa yang perusahaan gambarkan sebagai "bahan keras yang unik dan formulasi polimer," mereka memberikan perlindungan pecahan peluru dan dapat diperbaiki di lapangan.
Perlindungan tentara
SPS (Soldier Protection System) yang dikembangkan oleh 3M Ceradyne termasuk helm dan sisipan pelindung tubuh untuk Sistem Perlindungan Kepala Terpadu (IHPS) dan VTP (Perlindungan Tubuh Vital) - komponen ESAPI (Enhanced Small Arms Protective Insert) - sisipan yang ditingkatkan untuk perlindungan terhadap senjata kecil) dari sistem SPS.
Persyaratan IHPS mencakup bobot yang lebih ringan, perlindungan pendengaran pasif, dan perlindungan benturan tumpul yang ditingkatkan. Sistem ini juga mencakup aksesori seperti komponen untuk melindungi rahang bawah seorang prajurit, pelindung, dudukan untuk kacamata penglihatan malam, panduan untuk, misalnya, senter dan kamera, dan pelindung peluru modular tambahan. Kontrak, senilai lebih dari $ 7 juta, menyediakan pasokan sekitar 5.300 helm. Sementara itu, lebih dari 30.000 kit ESAPI - sisipan yang lebih ringan untuk pelindung tubuh - akan dikirimkan di bawah kontrak $ 36 juta. Produksi kedua kit ini dimulai pada tahun 2017.
Juga di bawah program SPS, KDH Defense memilih material SPECTRA SHIELD dan GOLD SHIELD Honeywell untuk lima subsistem, termasuk subsistem Torso and Extremity Protection (TEP) yang akan dipasok untuk proyek SPS. Sistem perlindungan TEP 26% lebih ringan, yang pada akhirnya mengurangi bobot sistem SPS sebesar 10%. KDH akan menggunakan SPECTRA SHIELD, yang didasarkan pada serat UHMWPE, dan GOLD SHIELD, berdasarkan serat aramid, dalam produknya sendiri untuk sistem ini.
serat SPECTRA
Honeywell menggunakan proses pemintalan dan penarikan serat polimer eksklusif untuk menanamkan bahan mentah UHMWPE ke dalam serat SPECTRA. Bahan ini 10 kali lebih kuat dari baja dalam hal berat, kekuatan spesifiknya 40% lebih tinggi dari serat aramid, memiliki titik leleh lebih tinggi daripada polietilen standar (150 ° C) dan ketahanan aus yang lebih besar dibandingkan dengan polimer lain, untuk misalnya poliester.
Bahan SPECTRA yang kuat dan kaku menunjukkan deformasi yang tinggi saat putus, yaitu meregang sangat kuat sebelum putus; sifat ini memungkinkan sejumlah besar energi tumbukan diserap. Honeywell mengklaim bahwa komposit serat SPECTRA berkinerja sangat baik di bawah dampak kecepatan tinggi seperti peluru senapan dan gelombang kejut. Menurut perusahaan, “Serat canggih kami bereaksi terhadap benturan dengan menghilangkan energi kinetik secara cepat dari zona tumbukan … juga memiliki peredam getaran yang baik, ketahanan yang baik terhadap deformasi berulang dan karakteristik gesekan internal yang sangat baik dari serat bersama dengan ketahanan yang sangat baik terhadap bahan kimia., air dan sinar UV."
Dalam teknologi SHIELD-nya, Honeywell menyebarkan untaian serat paralel dan mengikatnya bersama-sama dengan menghamilinya dengan resin canggih untuk membuat pita searah. Kemudian lapisan pita ini ditempatkan melintang pada sudut yang diinginkan dan pada suhu dan tekanan tertentu, disolder ke dalam struktur komposit. Untuk aplikasi yang dapat dipakai dengan lembut, lapisan ini dilaminasi antara dua lapisan film transparan yang tipis dan fleksibel. Karena serat tetap lurus dan paralel, serat tersebut menghilangkan energi benturan lebih efisien daripada jika ditenun menjadi kain tenun.
Short Bark Industries juga menggunakan SPECTRA SHIELD pada bodyguard BCS (Ballistic Combat Shirt) untuk sistem SPS TEP. Short Bark mengkhususkan diri dalam perlindungan lembut, pakaian taktis dan aksesoris.
Menurut Honeywell, tentara memilih elemen pelindung yang terbuat dari bahan-bahan ini setelah mereka menunjukkan kinerja yang unggul dibandingkan rekan-rekan serat aramid mereka.