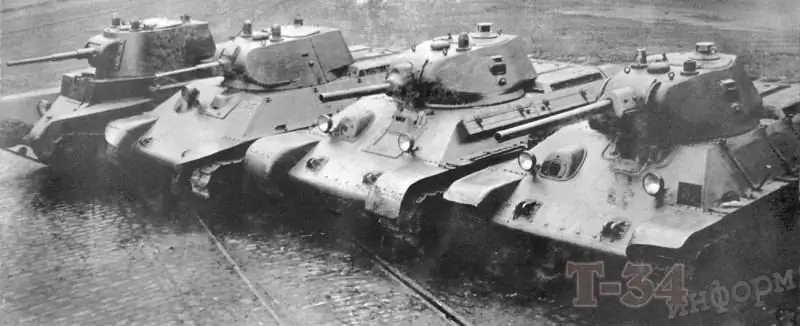
Menunggu perang
Masalah dengan produksi tank di Uni Soviet pada 1920-an dan 1930-an, terutama terkait dengan tidak tersedianya industri, sebagian dijelaskan oleh ketertinggalan industri lapis baja. Pada awal tahun 1932, hanya dua dari empat perusahaan yang direncanakan yang dapat melakukan smelt and roll armor. Ini adalah pabrik Izhora dan Mariupol. Karena persyaratan yang terlalu tinggi untuk kecepatan produksi (ini adalah tanda waktu itu), pabrik-pabrik ini secara kronis berada di belakang rencana. Jadi, di salah satu perusahaan tertua di negara itu, pabrik Izhora di kota Kolpino, dalam setahun mereka hanya mampu menguasai 38% dari rencana, dan di Mariupol di pabrik Ilyich - hanya seperempat. Ini sebagian besar disebabkan oleh produksi baju besi heterogen yang disemen kompleks, yang mereka tahu cara membuatnya di negara kita sejak 1910. Jenis baju besi yang serupa diperlukan untuk menahan proyektil dan peluru berkepala tajam, yang tidak disediakan oleh kekerasan sedang dan rendah yang homogen. Pada saat itu, armor yang disemen dibagi menjadi dua tingkatan: tempered rendah yang disemen secara sepihak dengan sisi belakang yang cukup keras dan, dalam versi kedua, dengan sisi belakang yang keras sedang. Pada dasarnya, untuk produksi "sandwich" seperti itu diperlukan baja kromium-molibdenum dan kromium-nikel-molibdenum, yang membutuhkan aditif ferroalloy impor yang langka. Elemen paduan utama baja ini adalah kromium (1, 5-2, 5%), yang mendorong karburisasi intensif dan pencapaian kekerasan tinggi dari lapisan semen setelah pendinginan. Upaya untuk menggunakan mangan dan silikon dalam negeri untuk baja yang dikeraskan dengan kasing alih-alih kromium impor menghasilkan hasil negatif. Ketika dicampur dengan mangan, terungkap bahwa baja rentan terhadap pertumbuhan butir pada suhu karburasi (920-950 derajat Celcius), terutama dengan eksposur lama yang diperlukan untuk karburasi hingga kedalaman yang luar biasa. Koreksi lapisan karburasi yang terlalu panas selama sementasi menimbulkan kesulitan yang signifikan dan dikaitkan dengan kebutuhan untuk menerapkan beberapa rekristalisasi, yang menyebabkan dekarburisasi yang signifikan pada lapisan semen dan timah lembaran, dan juga tidak menguntungkan secara ekonomi. Namun demikian, hingga awal 30-an, baju besi yang disemen digunakan baik dalam penerbangan maupun dalam pembuatan tank. Di pesawat, pelat baja hingga 13 mm disemen, seperti pelindung tangki hingga 30 mm. Ada juga pengembangan baju besi semen 20 mm yang tahan peluru, yang tidak melampaui pengembangan eksperimental. Armor seperti itu pasti harus sangat besar, yang hanya membutuhkan sumber daya raksasa untuk pengembangan produksi.
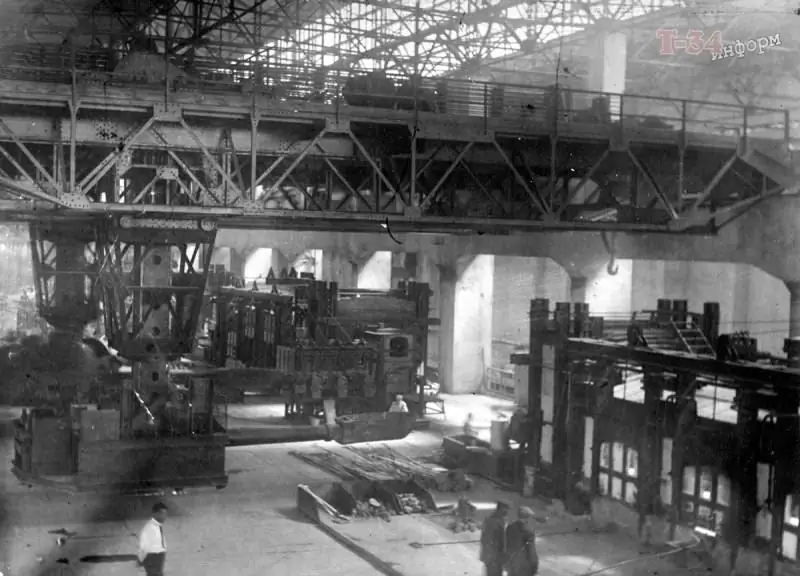
Terlepas dari kesulitan seperti itu dengan produksi baju besi yang disemen, lambung tangki T-28 hampir sepenuhnya terbuat dari itu. Namun secara bertahap, industri dalam negeri meninggalkan teknologi untuk menyemen pelat baja, sebagian besar karena penolakan yang sangat tinggi. Mengingat rencana produksi yang diminta oleh pemerintah dan komisariat rakyat khusus, ini sama sekali tidak mengejutkan. Pabrik Izhora adalah yang pertama beralih ke baju besi baru, setelah menguasai peleburan baju besi kromium-silika-mangan "PI" yang sangat keras. Di Mariupol, mereka menguasai "MI" mangan yang heterogen. Negara secara bertahap beralih ke pengalamannya sendiri dalam merancang baju besi. Sampai saat itu, itu didasarkan pada teknologi asing (terutama Inggris). Penolakan untuk menyemen baju besi membuat lembaran lebih tebal dengan ketahanan baju besi yang sama. Jadi, alih-alih baju besi semen 10 dan 13 mm, lambung T-26 harus dilas dari lembaran baja Izhora "PI" 15 mm. Dalam hal ini, berat tangki adalah 800 kilogram. Perlu dicatat bahwa transisi dari baja semen yang mahal ke teknologi baju besi homogen yang relatif murah ternyata sangat berguna di masa perang. Jika ini tidak terjadi pada tahun-tahun sebelum perang, pengembangan peleburan dan penggulungan jenis baju besi yang mahal tidak akan mungkin terjadi karena evakuasi perusahaan pada tahun 1941-1942.
Sejak tahun-tahun sebelum perang, peran utama dalam pencarian dan penelitian jenis baju besi baru dimainkan oleh "Armor Institute" TsNII-48, yang sekarang dikenal sebagai NRC "Kurchatov Institute" - TsNII KM "Prometheus". Tim insinyur dan ilmuwan TsNII-48 menentukan arah utama industri baju besi domestik. Dalam dekade terakhir sebelum perang, kemunculan artileri penusuk lapis baja di luar negeri dari kaliber 20 hingga 50 mm menjadi tantangan serius. Ini memaksa para pengembang untuk mencari resep baru untuk baju besi tangki memasak.
Kelahiran 8C
Ganti pelindung yang disemen yang tahan terhadap proyektil dan peluru berkepala tajam pada kendaraan lapis baja ringan dan sedang hanya dengan baja kekerasan tinggi. Dan ini berhasil dikuasai oleh ahli metalurgi domestik. Lambung kendaraan lapis baja BA-10, tank ringan T-60 (ketebalan lapis baja 15 mm, frontal - 35 mm), T-26 (ketebalan lapis baja 15 mm) dan, tentu saja, tank menengah T-34 (ketebalan lapis baja 45 mm). Jerman juga memiliki prioritas baju besi kekerasan tinggi. Faktanya, semua armor (dimulai dengan helm infanteri dan diakhiri dengan struktur pelindung penerbangan) akhirnya menjadi memiliki kekerasan tinggi, menggantikan yang disemen. Mungkin hanya KV berat yang mampu membeli armor dengan kekerasan sedang, tetapi ini harus dibayar dengan ketebalan lembaran yang lebih besar dan massa akhir tangki.
Baja lapis baja 8C, dasar pertahanan anti-meriam tank T-34, menjadi mahkota kreativitas nyata para ahli metalurgi domestik. Perlu dicatat bahwa produksi baju besi 8C pada tahun-tahun sebelum perang dan selama Perang Patriotik Hebat adalah dua proses yang sangat berbeda. Bahkan untuk industri sebelum perang Uni Soviet, produksi 8C adalah proses yang rumit dan mahal. Mereka berhasil menguasainya hanya di Mariupol. Komposisi kimia 8C: C - 0,22-0,28%, Mn - 1,0-1,5%, Si - 1,1-1,6%, Cr - 0,7-1,0%, Ni - 1,0-1,5%, Mo - 0,15-0,25%, P - kurang dari 0,035% dan S - kurang dari 0,03%. Untuk peleburan, diperlukan tungku perapian terbuka dengan kapasitas hingga 180 ton, menuangkan baju besi masa depan ke dalam cetakan yang relatif kecil masing-masing 7, 4 ton. Deoksidasi paduan cair (penghilangan kelebihan oksigen) dalam tungku dilakukan dengan metode difusi yang mahal menggunakan karbon atau silikon. Ingot yang sudah jadi dikeluarkan dari cetakan dan digulung, diikuti dengan pendinginan lambat. Di masa depan, baju besi masa depan kembali dipanaskan hingga 650-680 derajat dan didinginkan di udara: itu adalah liburan tinggi, dirancang untuk memberikan plastisitas baja dan mengurangi kerapuhan. Hanya setelah itu lembaran baja dapat diproses secara mekanis, karena pengerasan berikutnya dan temper rendah pada 250 derajat membuatnya terlalu keras. Faktanya, setelah prosedur pengerasan akhir dengan 8C, sulit untuk melakukan apa pun selain mengelas bodinya. Tapi di sini juga, ada kesulitan mendasar. Tegangan pengelasan internal yang signifikan yang timbul dari daktilitas rendah dari logam pelindung 8C, terutama dengan kualitasnya yang rendah, yang mengarah pada pembentukan retakan, yang sering meningkat seiring waktu. Retakan di sekitar jahitan bisa terbentuk bahkan 100 hari setelah tangki diproduksi. Ini menjadi momok nyata bagi pembangunan tank Uni Soviet selama perang. Dan pada periode sebelum perang, cara paling efektif untuk mencegah pembentukan retakan selama pengelasan baju besi 8C adalah penggunaan pemanasan lokal awal dari zona pengelasan hingga suhu 250-280 derajat. Untuk tujuan ini, TsNII-48 mengembangkan induktor khusus.
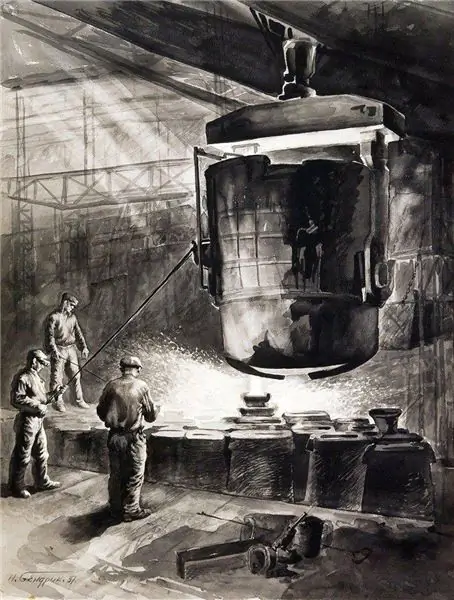
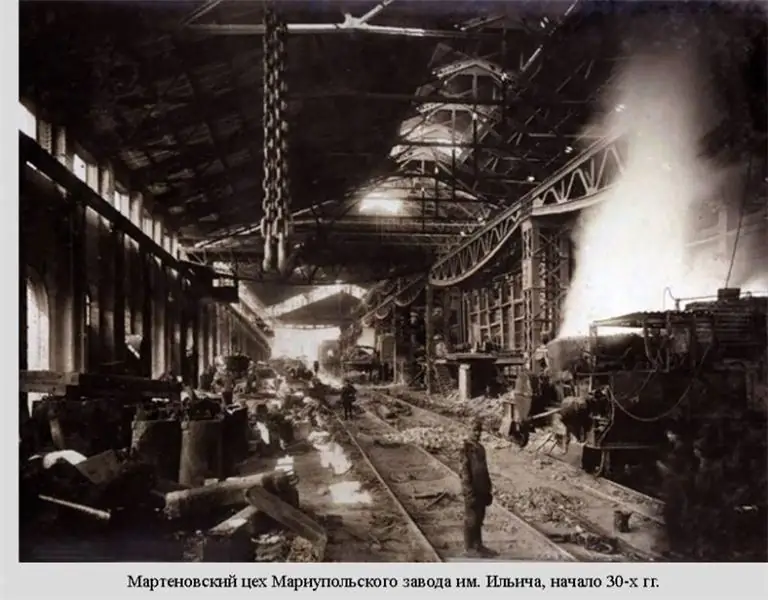
8C bukan satu-satunya grade baja untuk armor T-34. Jika ada kesempatan, itu ditukar dengan varietas lain yang lebih murah. Pada periode sebelum perang, TsNII-48 mengembangkan pelindung struktural 2P, yang produksinya secara signifikan menghemat energi dan menyederhanakan penggulungan lembaran. Komposisi kimia 2P: C - 0,23-0,29%, Mn - 1,2-1,6%, Si - 1,2-1,6%, Cr - kurang dari 0,3%, Ni - kurang dari 0, 5%, Mo - 0,15-0,25%, P - kurang dari 0,035% dan S - kurang dari 0,03%. Seperti yang Anda lihat, penghematan utama adalah nikel dan kromium yang langka. Pada saat yang sama, toleransi yang sangat ketat untuk keberadaan fosfor dan belerang tetap tidak berubah untuk 2P, yang, tentu saja, sulit dicapai, terutama di masa perang. Terlepas dari semua penyederhanaan, pelindung struktural yang terbuat dari baja 2P masih menjalani perlakuan panas - pendinginan dan tempering tinggi, yang secara signifikan memuat peralatan termal yang diperlukan untuk perlakuan panas pada bagian pelindung tangki yang lebih kritis, dan juga secara signifikan meningkatkan siklus produksi. Selama perang, spesialis TsNII-48 mampu mengembangkan teknologi untuk mendapatkan baja serupa, yang produksinya membebaskan sumber daya untuk baju besi utama 8C.